Home / Air Cooled Heat Exchangers
Air Cooled Heat Exchanger
- Forced Draft
- Induced Draft
- High Temperature / High Pressure
- Special Configuration
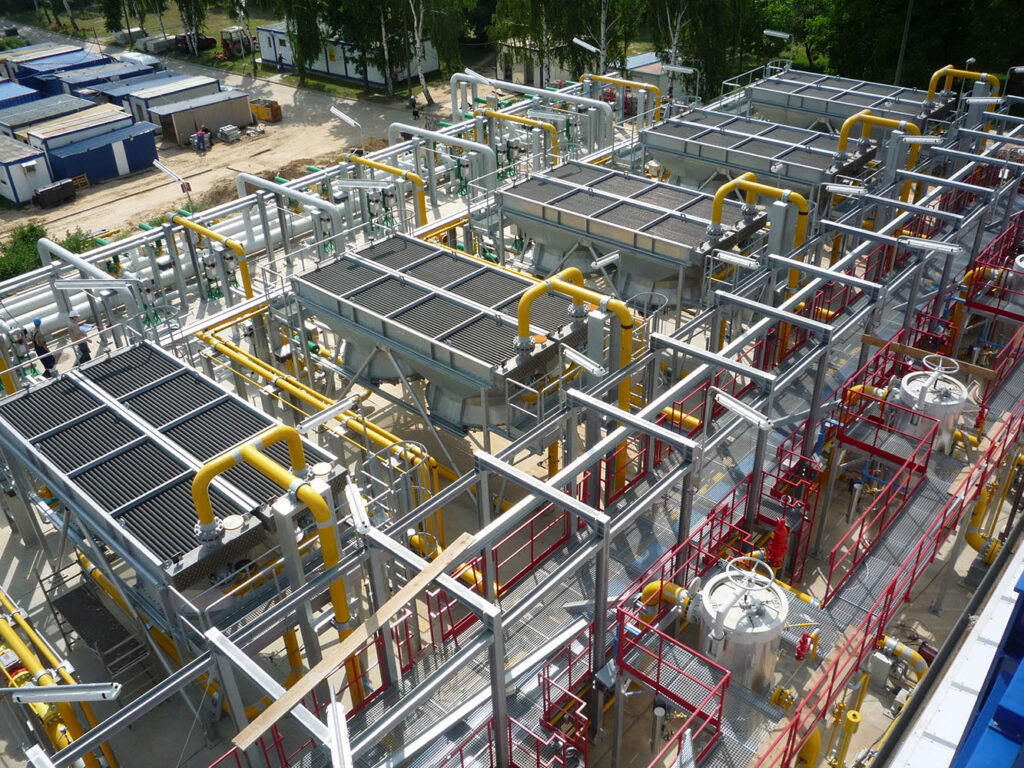
The most evident advantages of air cooled heat exchangers are:
- Prevention of thermal and chemical pollution of cooling fluids
- Flexibility for any plant location and plot plan arrangement
- Reduction of maintenance costs
- Easy installation by bolted assembly
- Lower environmental impact than S&T heat exchangers
We have the experience, engineering expertise and manufacturing capabilities to be your preferred choice for air cooled heat exchangers. We provide our customers with high-quality, cost-effective and reliable air cooled heat exchanger and technical support.
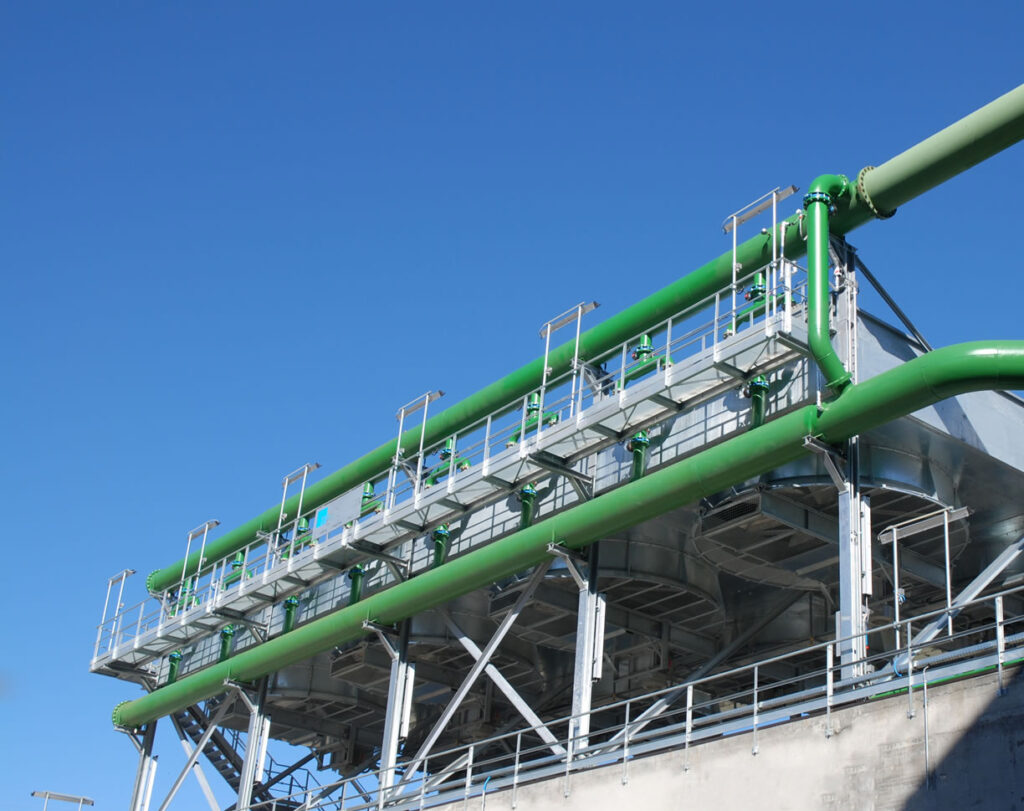
Forced draft/Induced draft
Forced draft units are easier to manufacture and to maintain. The tube bundle is mounted on top of the plenum, so it can be easily removed and replaced. The fan shaft is short, since it does not have to extent from the drive unit through the tube bundle and plenum to the fan, as in an induced draft design.
Forced draft units require slightly less horsepower since the fan are moving a lower volume of air at the inlet than they would at the outlet. If the process fluid is very hot, the cooling air is hot at the outlet. This could cause problems with some fans or fan pitch actuators if the fan is exposed to very hot exhaust air. Since forced draft coolers do not have the fans exposed to hot exhaust air, they are a better choice in such cases.
However, induced draft units have some advantages, too. A common problem with forced draft coolers is accidental warm air recirculation. This happens when the hot exhaust air is pulled back in to the fans. Since a forced draft cooler has a low air velocity at the exhaust from the bundle and a high velocity through the fan, a low pressure area is created around the fan, causing the hot air to be pulled over the side or end of the bay.
For this same reason, there should never be a small space between the bays of a bank of forced-draft cooler. Induced draft cooler have a high exhaust air velocity through the fan, and a lower velocity into the face of the tube bundle below. This tends to minimize the probability of accidental air recirculation. Also an induced draft plenum does not have to support the tube bundle so some weight can often be saved in this area.
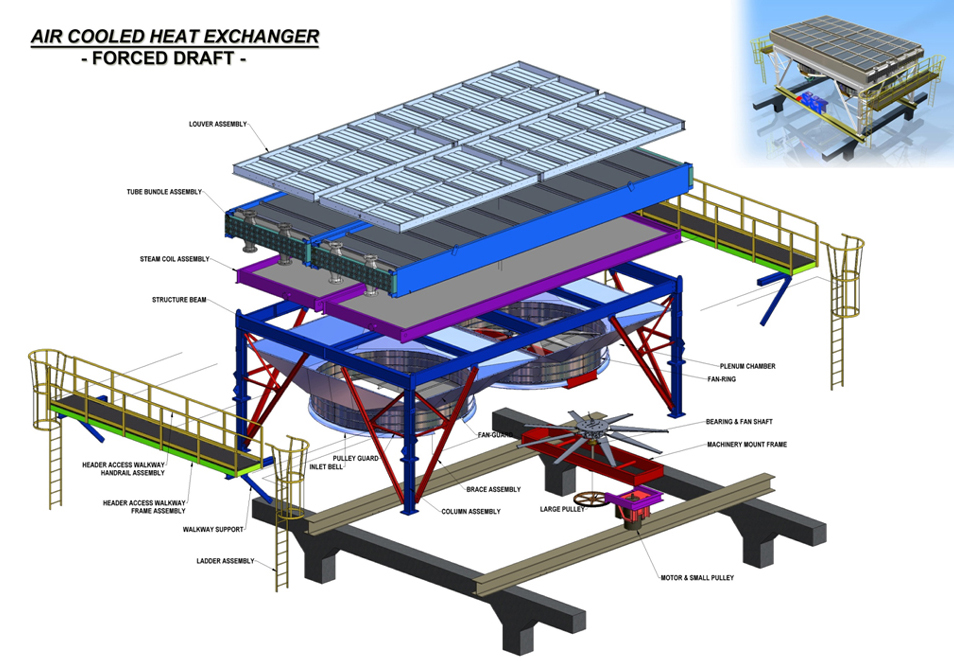
FORCED DRAFT
The tube bundle is mounted on top of the plenum, so it can be easily removed and replaced. The fan shaft is short, since it does not have to extent from the drive unit through the tube bundle and plenum to the fan.
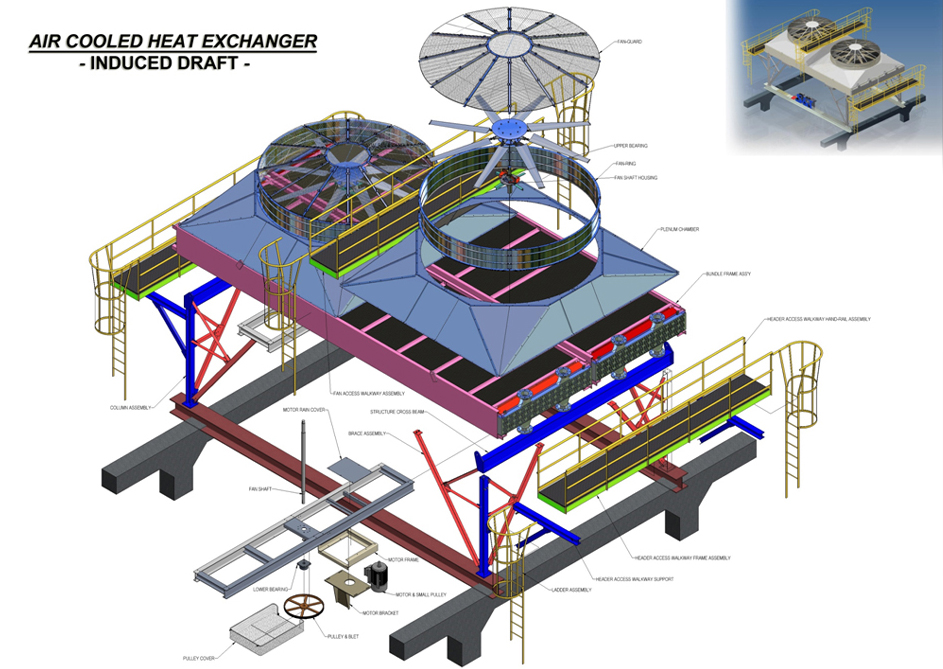
INDUCED DRAFT
The tube bundle is mounted under the plenum. The fan shaft is long, since it does have to extent from the drive unit through the tube bundle and plenum to the fan.
Finned Tube
The tubes can be of virtually any material available, such as carbon steel, stainless steel, Admiralty brass, or more exotic alloys. The fins are almost always of aluminum material.
Extruded fins are made by putting an aluminum sleeve over the tube, then passing the tube through a machine which has rollers which squish the aluminum out to form fins. The end result is a fin which has extremely good contact with the tube, and no crevices to allow corrosion to start on the tube OD. Extruded fins are often used in coastal locations or on offshore platforms for this reason.
L-footed type or helically wrapped fintube, are used where the process temperatures are below about 350 deg. F. The embedded fins have the highest temperature capabilities. They are made by a process which cuts a helical groove in the OD of the tube, wraps the fin into the groove, then rolls the upset metal from the tube back against the fin to lock it into place. The tube wall must be thicker with embedded fins because of the groove.
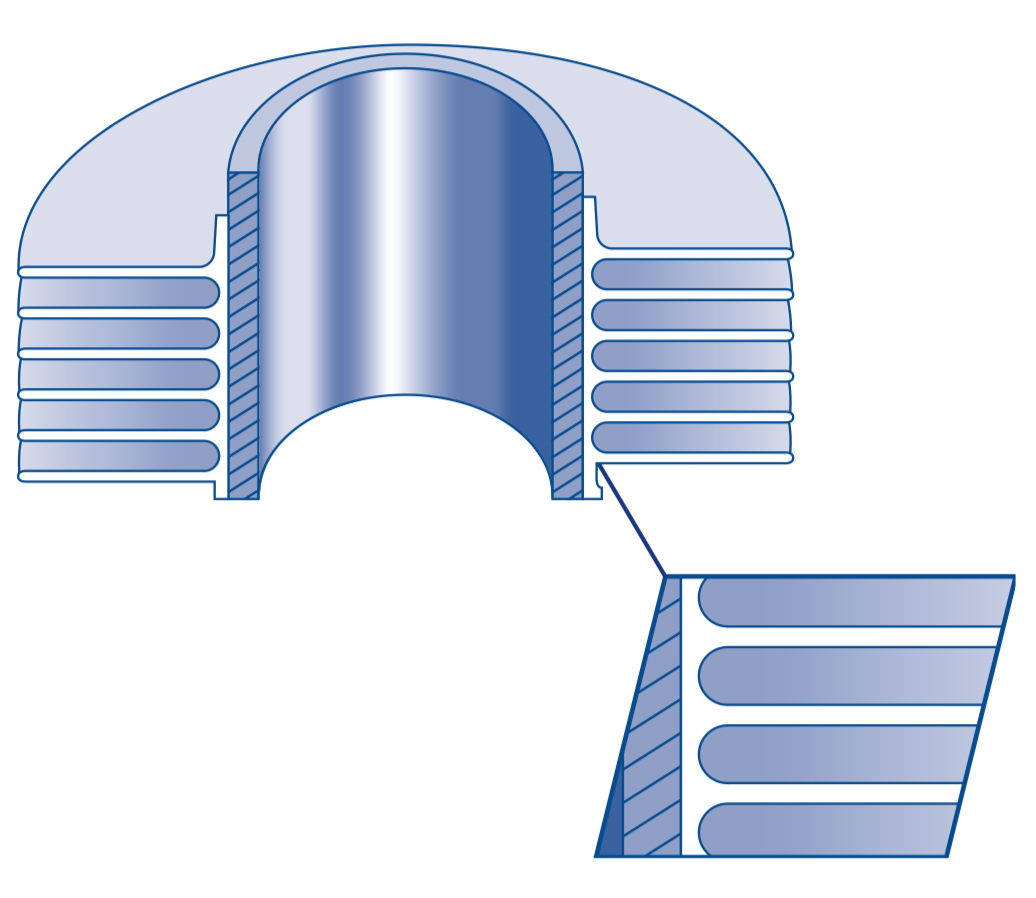
EXTRUDED
Extruded fins are made by putting an aluminum sleeve over the tube, then passing the tube through a machine which has rollers which squish the aluminum out to form fins.
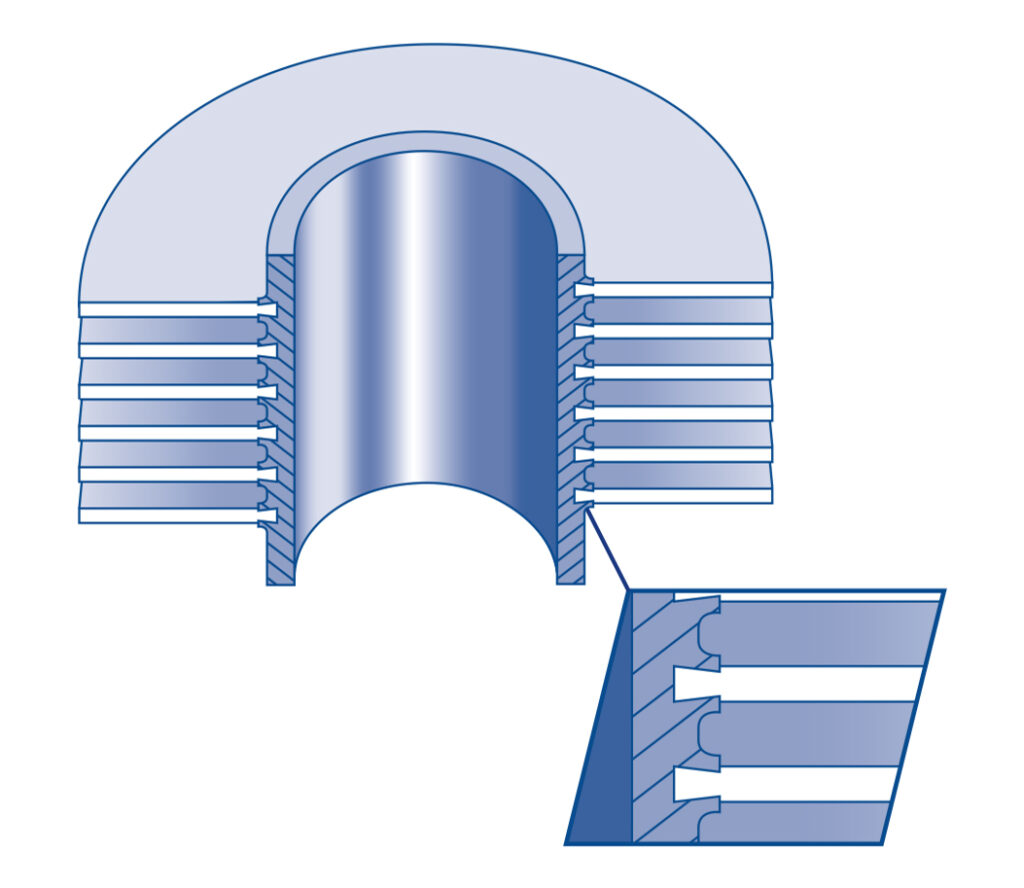
EMBEDDED
The embedded fins have the highest temperature capabilities. They are made by a process which cuts a helical groove in the OD of the tube, wraps the fin into the groove.
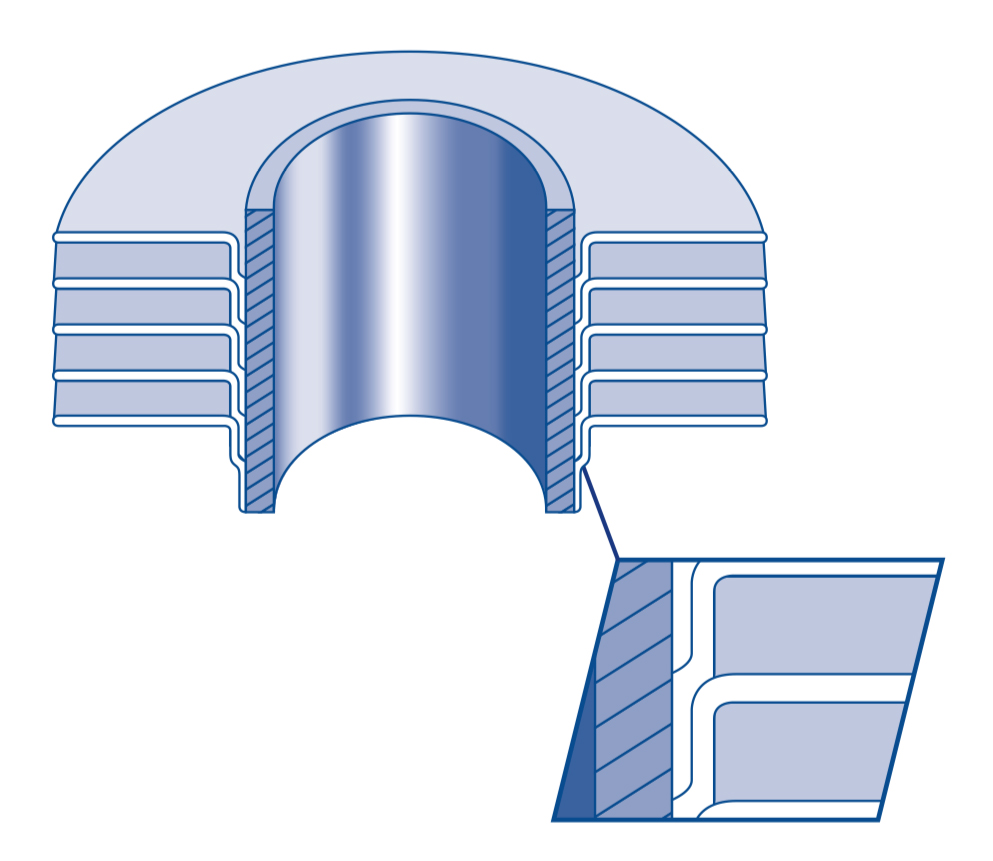
L-FOOTED
L-footed type or helically wrapped fin-tube, are used where the process temperatures are below about 350 deg.
Applications for Air Cooled Heat Exchangers
ACHEs are primarily used in the petrochemical, refining, natural gas processing and power generation industries:
- Hydrocarbon processing
- Petrochemical processing
- Gas compression (stage cooling)
- Gas transmission
- Gas condensing
- Refinery process cooling
- Industrial cooling applications
- Refrigerant condensing
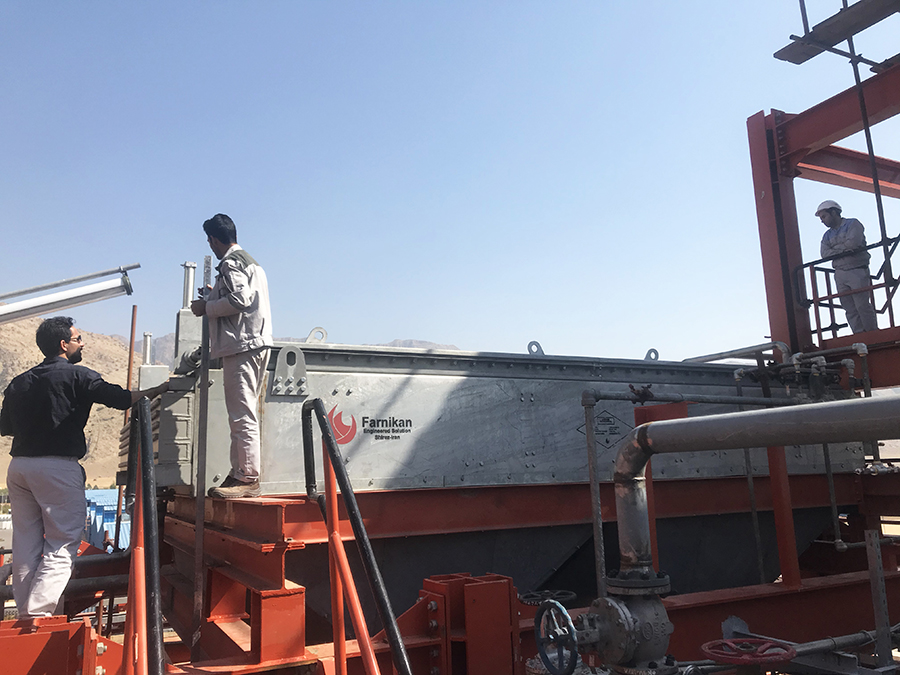
Air Cooler Headers
Headers are the boxes at the ends of the tubes which distribute the fluid from the piping to the tubes. Almost all headers on air-cooled exchangers are welded rectangular boxes. A vast majority of the headers are of the plug type. This means that there is a shoulder plug opposite each tube which allows access for inspection and cleaning of individual tubes. They can also be used to plug a leaking tube. The other common type of header is the cover plate or bonnet type. These are usually used in low pressure applications (say below 150 PSIG) where complete tube access is desired. This usually means applications where fouling is a potential problem and the tube bundle may require occasional internal cleaning. As the name implies, these have a removable plate on the back side of the header opposite the tubes. The cover plate is attached to the header by a set of studs or through- bolts to a flange around the perimeter of the header.
A bonnet header is similar, but opposite in construction. The whole header or bonnet bolts to the tubesheet and comes off. Bonnet headers are sometimes used where the corrosion potential of the process fluid is very high and the tubesheet material is some kind of expensive exotic alloy, such as titanium.
Types of Headers:
- Box Type Header
- Bonnet Type Header
- Cover Type Header
- Manifold Type Header
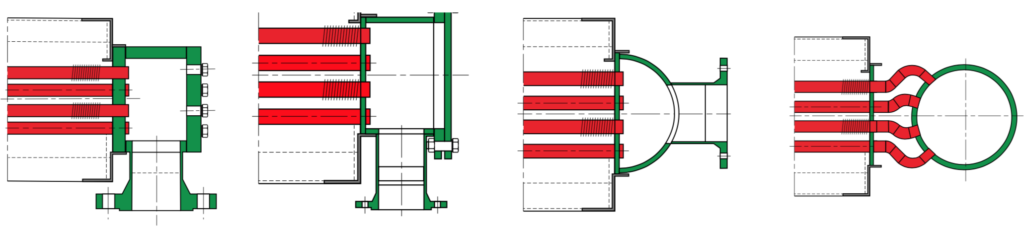
Blowing System
The fans are usually driven be electric motors through some type of speed reducer. The speed reducers are usually either V-belts, HTD drives, or right angle gears. The fan drive assembly is supported by a steel mechanical drive support system. They usually include a vibration switch on each fan to automatically shut down a fan which has become imbalanced for some reason
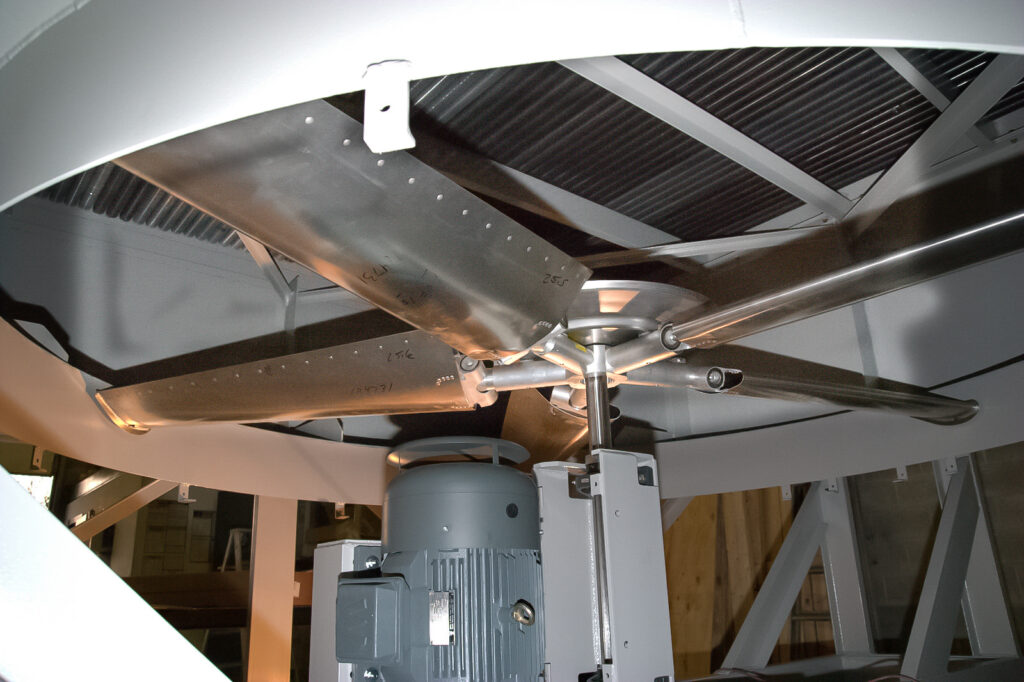
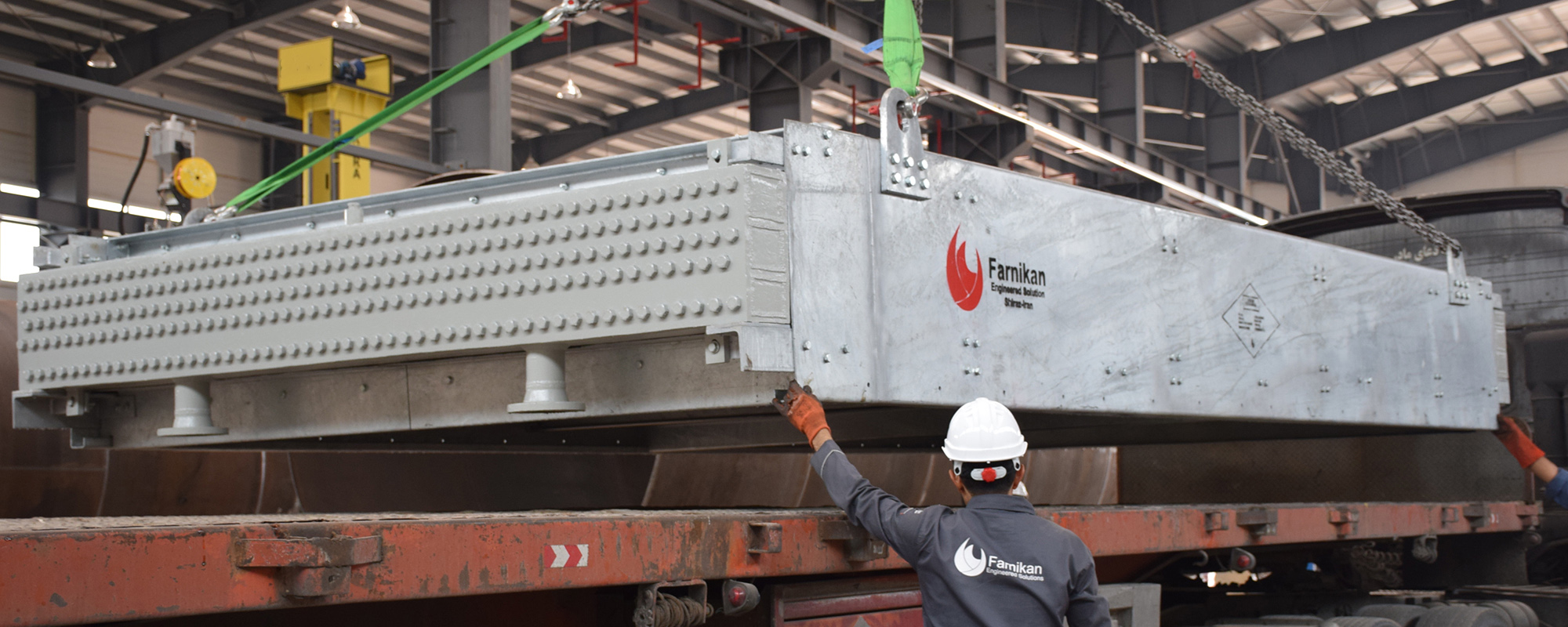
Heat Transfer Principle
Process Criteria
How does an Air Cooled Heat Exchanger work?
An ACHE is a device for rejecting heat from a fluid directly to ambient air. This is in contrast to rejecting heat to water and then rejecting it to air, as with a shell and tube heat exchanger and a wet cooling tower system. The obvious advantage of an ACHE is that it does not require water, which means that plants requiring large cooling capacities need not be located near a supply of cooling water. An ACHE consists of the following components:
- One or more bundles of heat transfer surface.
- An air-moving device, such as a fan, blower, or stack.
- Unless it is natural draft, a driver and power transmission to mechanically rotate the fan or blower.
- A plenum between the bundle or bundles and the air-moving device.
- A support structure high enough to allow air to enter beneath the ACHE at a reasonable rate.
- Optional header and fan maintenance walkways with ladders to grade.
- Optional louvers for process outlet temperature control.
- Optional recirculation ducts and chambers for protection against freezing or solidification of high pour point fluids in cold weather.
- Optional variable pitch fan hub for temperature control and power saving
Box-Tye Tube Bondle
Lorestan Petrochemical co
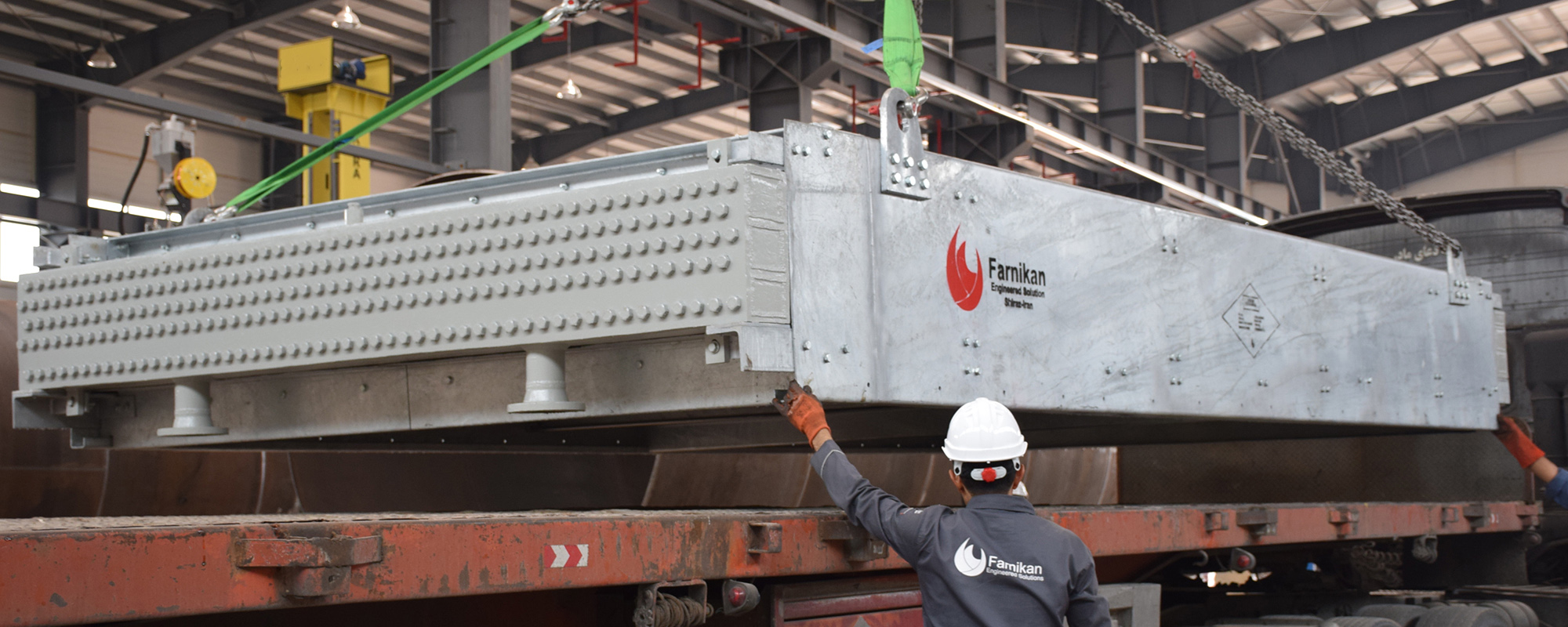