Home / Fabrication
Fabrication
Our multi-capable facilities back our assurance that your fabrication is carried out and delivered in full accordance with to client requirements. Our steelwork and metal fabrication arm provides comprehensive solutions and can accommodate customers across a wide range of industries, from simple steel structure fabrication to virtually any pressurized equipment in versatile ferrous / non-ferrous materials. All of these capabilities and services are backed up by in-house robust quality control programs, fully audited by our holistic quality assurance procedures and plans.
- Pre-Fabrication
- Welding
- Assembly
- Heat Treatment
- Testing & Verification
- Painting and Delivery
Our fabrication or fabrication management services are the preferred choice for those clients who seek for accurate, agile and precise manufacturing of equipment serving the Oil & Gas, Refineries, Petrochemicals and Power Sectors in Iran. Our commitment to the clients is proven by the quality management system & Occupation Health & Safety Management System certifications.
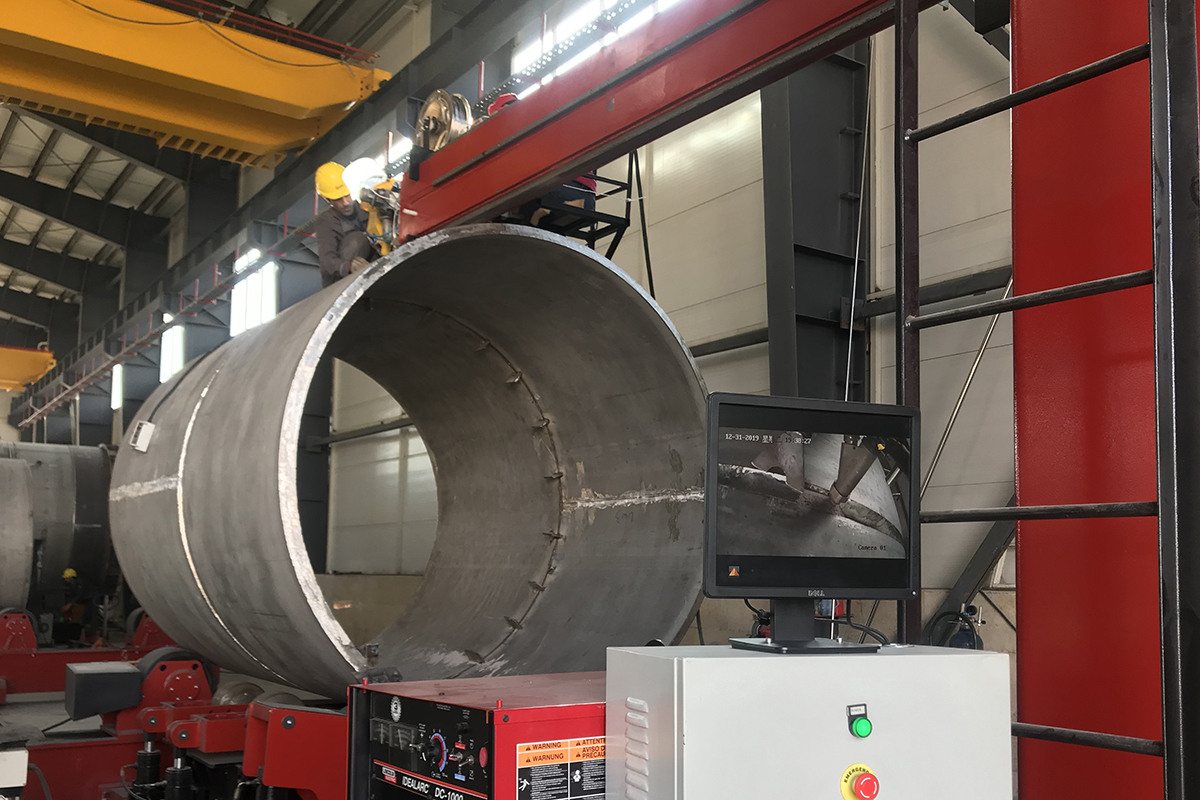
SUBMERGED ARC Welding
Submerged arc welding is commonly used in fabrication line where thick steel sheets are involved or where long welds are required. The process consists in creating a welded joint between steel components using an electric arc submerged beneath a layer of powdered flux.
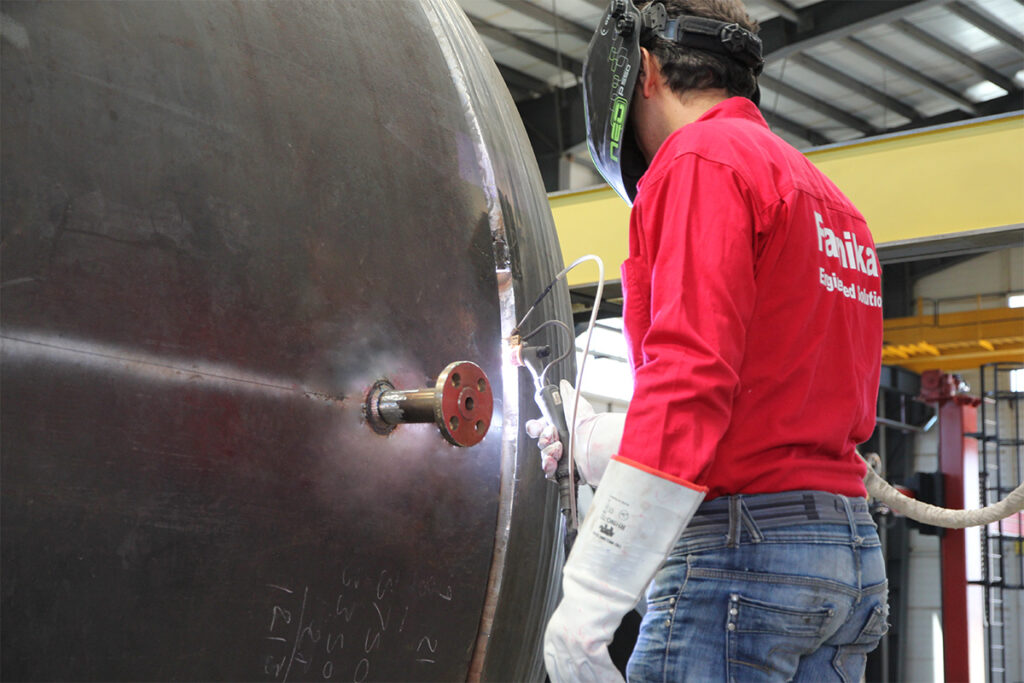
TIG WELDING
TIG stands for tungsten inert gas and is technically called gas tungsten arc welding (GTAW). The process uses a non-consumable tungsten electrode that delivers the current to the welding arc. The tungsten and weld puddle are protected and cooled with an inert gas, typically argon.
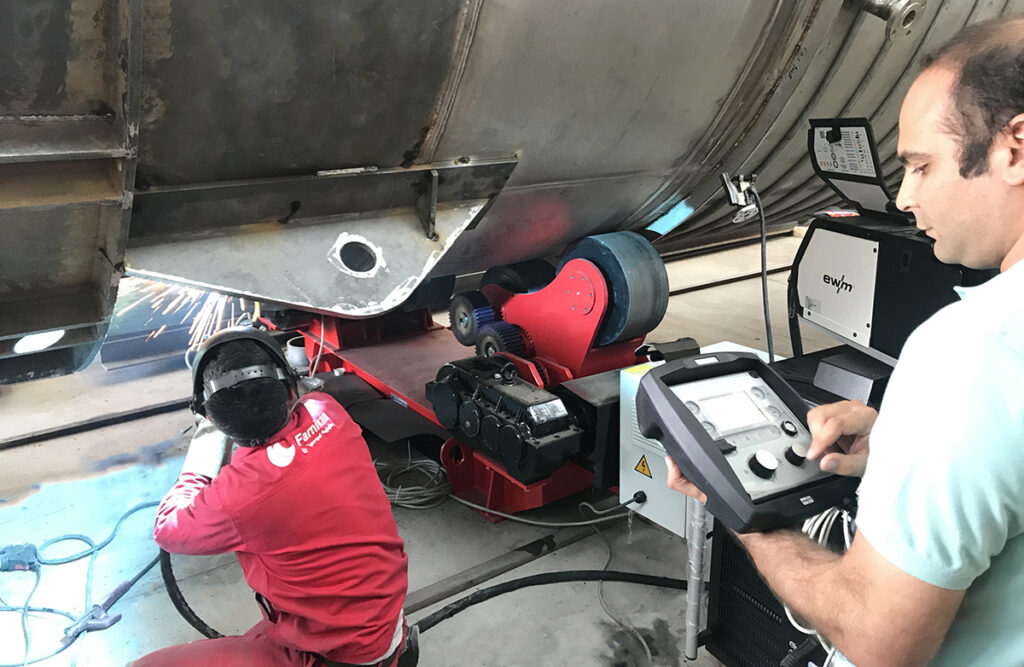
MIG/MAG
Metal Inert Gas (MIG) and Metal Active Gas (MAG) welding are gas metal arc welding (GMAW) processes that use heat created from a DC electric arc between a consumable metal electrode and a workpiece which melt together to create a weld pool that fuses to form a join.
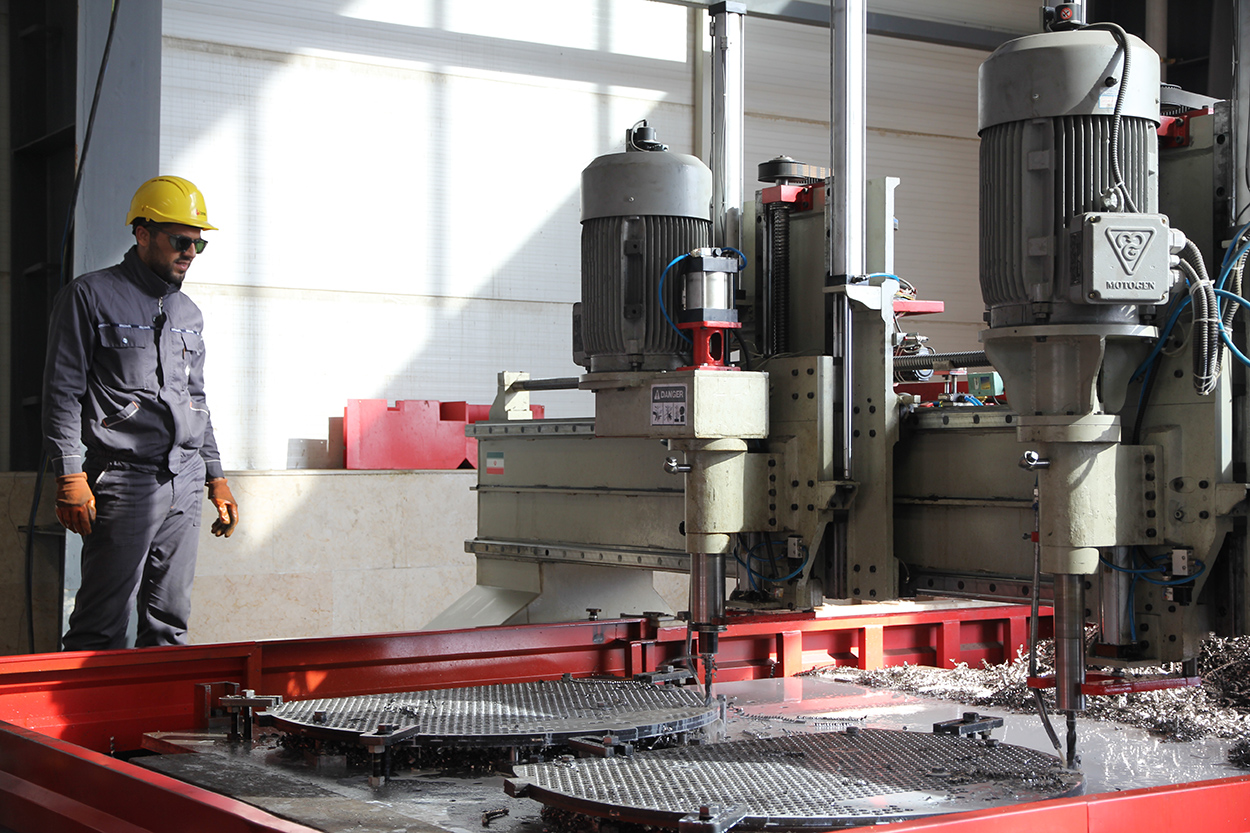
CNC Drilling
We use CNC drilling machine for drilling, milling, grooving and reaming of tube sheet and drilling of baffles to be used for our heat exchangers. Both of carbide and twist drills can be equipped with, as well as the function of chip blow and clean.
The machine utilized twin spindle for more productivity and speed of production.
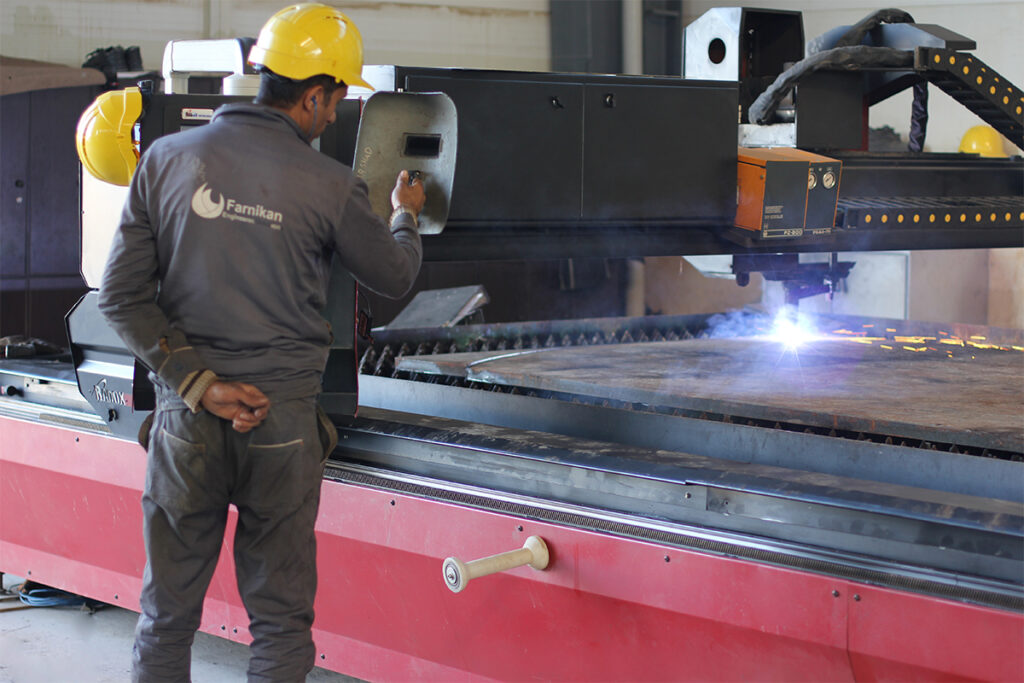
CNC CUTTING
Our CNC cutting machine is equipped with OXY Fuel as well as powerful German plasma torch for cutting complex shapes based on CAD Drawings. Utilizing this machine and other cutting machines we can cut thick plates made of Carbon Steel, Stainless Steel, and other non-ferrous materials. As machine is controlled by CNC, accuracy is at highest level for production of process equipment.
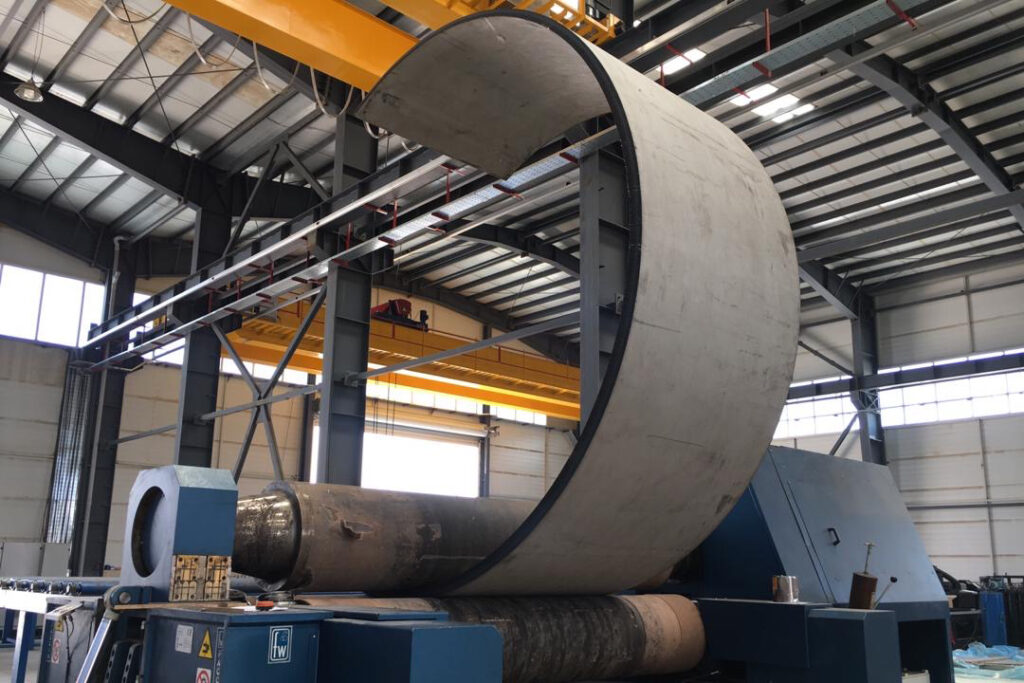
ROLL BENDING
We use modern 4-roll bending machine and one of the most advanced and powerful model of electronic 3-roll bending roll, HAV combines rolling power and maximum pre-bending precision, assuring very high performance in less time. Our machines are suited to rolling processes for thick plates used for production of pressure vessels, reactors, heat exchangers and others.
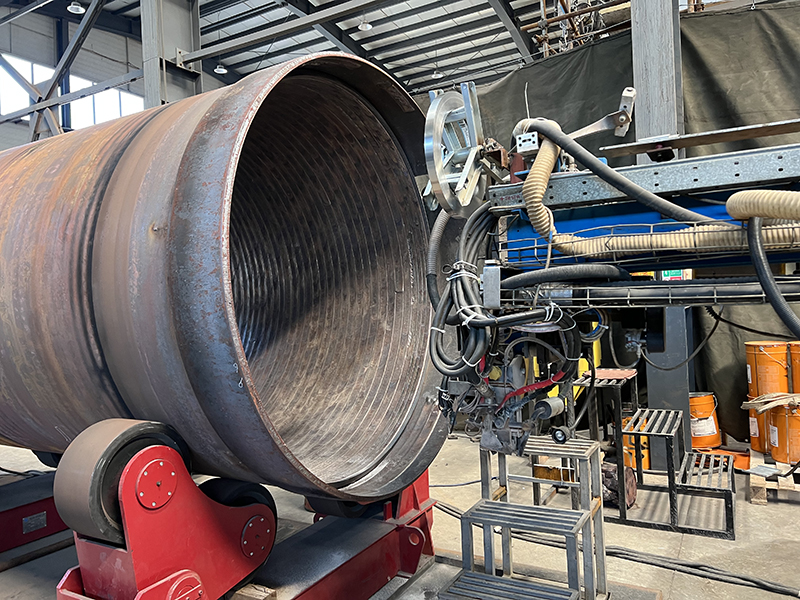
ESW Cladding
Farnikan uses the latest ESAB ESW / LINCOLN ESW strip cladding technology to perform high quality and efficient weld overlay wide strip cladding for internal surface of process rectors and pressure vessels.
Depending on size and service we are able to make cladding by strips: 30 x 0.5 mm / 60 x 0.5 mm / 90 x 0.5 mm.
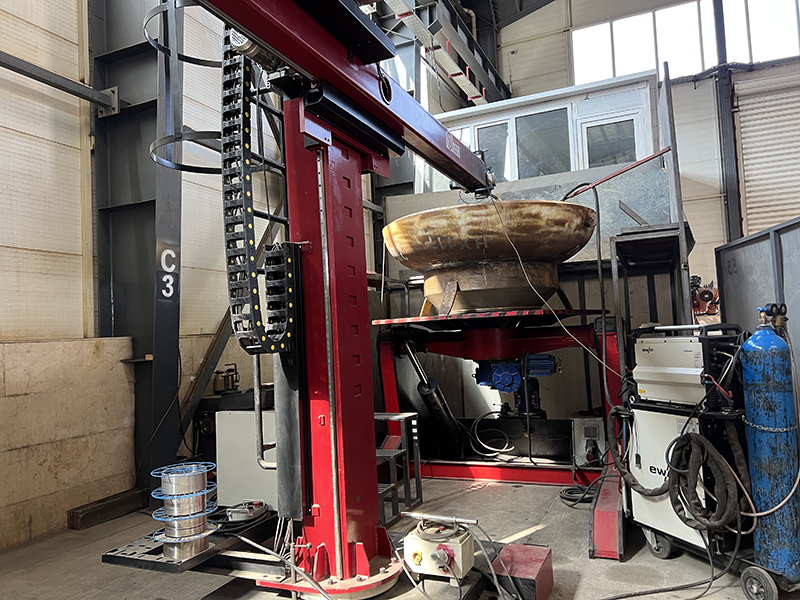
FLANGE CLADDING
We use hot-wire tig welding tools for cladding inside of pipes as flanges. Cladding flanges make use of a weld overlay cladding technology process that builds up the corrosion resistant alloy (CRA) layer on the welded parts of pipes and other piping components (e.g., valves, flanges). It protects the piping system’s integrity, and provides a low cost and long-term solution.
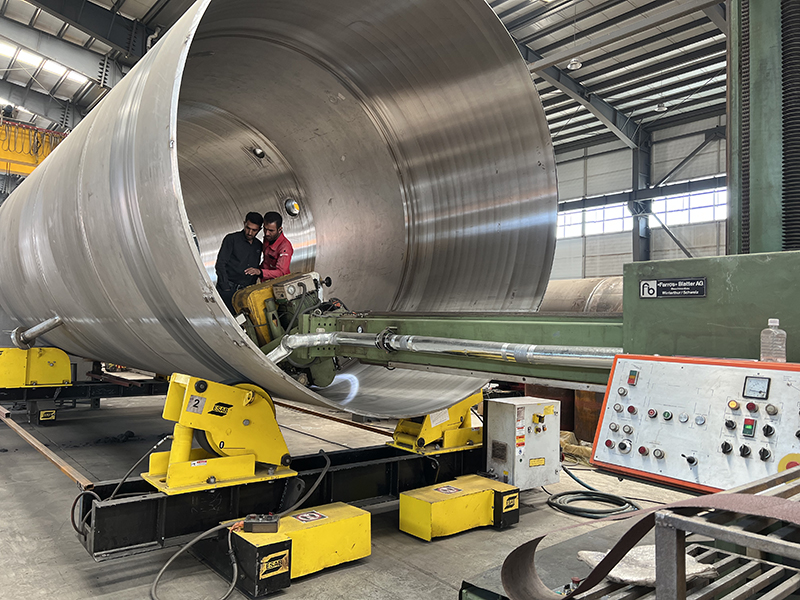
SURFACE POLISHING
We use one of the most modern mechanical polishing tools for internal surface polishing of those applications which needs certain level of finishing texture. Mechanical polishing is performed in steps with progressively finer abrasives until the desired smoothness is achieved. The precision polishing process removes material and plastically deforms the surface while it alters the macroscopic and microscopic surface texture.
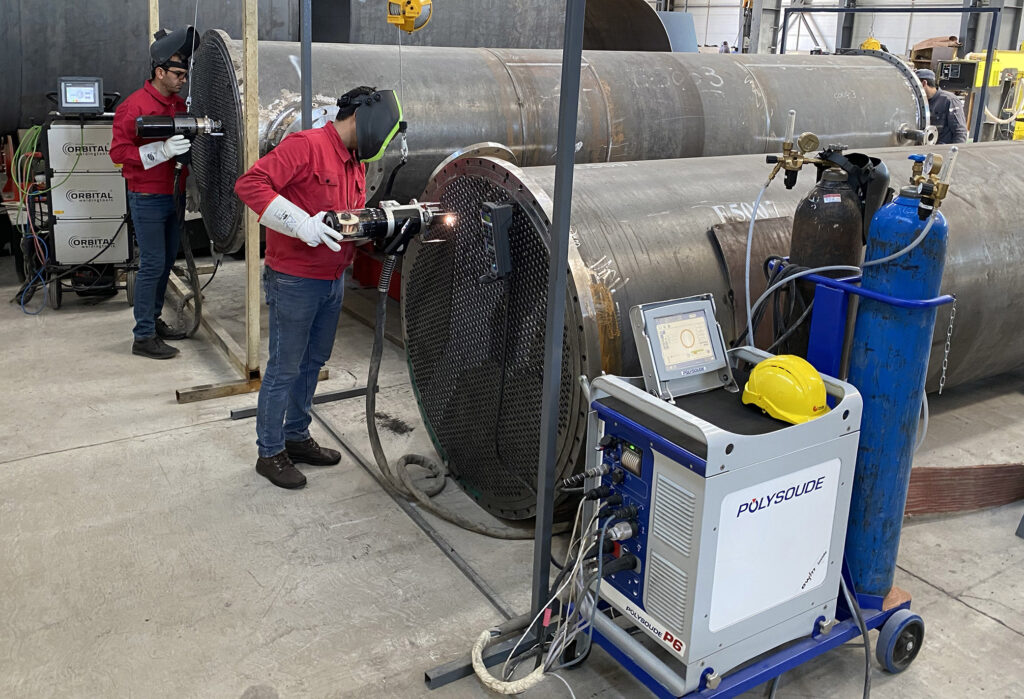
Orbital Welding
Tube to Tubesheet welding for autogenous or with filler wire welding.
We utilize the most advanced technology by state of art automatic orbital welding machines for tube to tubesheet welding. Weld heads can be configured with a wide selection of torches and configurations to match all common tube sheet designs. Tube configurations can be flush, recessed or projected above the tubesheet or even behind tube sheet (IBW). We use our automatic computer controlled machines to weld different metals and alloys. Most of the tube diameters measure between 19.05 mm (3/4″) and 50.8 mm (2″) with wall thicknesses between 1.65 mm and 4.5 mm.
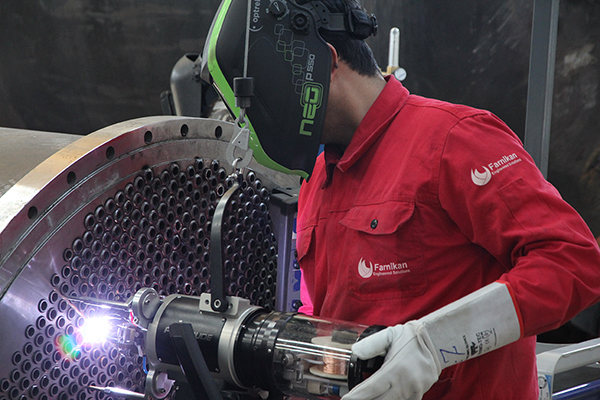
HEAT EXCHANGER
We utilize the most advanced technology by state of art automatic orbital welding machines for tube to tubesheet welding. Weld heads can be configured with a wide selection of torches and configurations to match all common tube sheet designs.

AIR COOLER
We utilize the special orbital welding tools for welding of tube to tubesheet in air cooler header box. Weld heads can be configured with a wide selection of torches and configurations to match all common tube sheet designs.

INNER BORE WELDING
In IBW Heat Exchangers, the tube does not pass through the tubesheet but rather is welded to a short stub machined on the tube side of the tube-sheet. We have special tools for such innovative method.
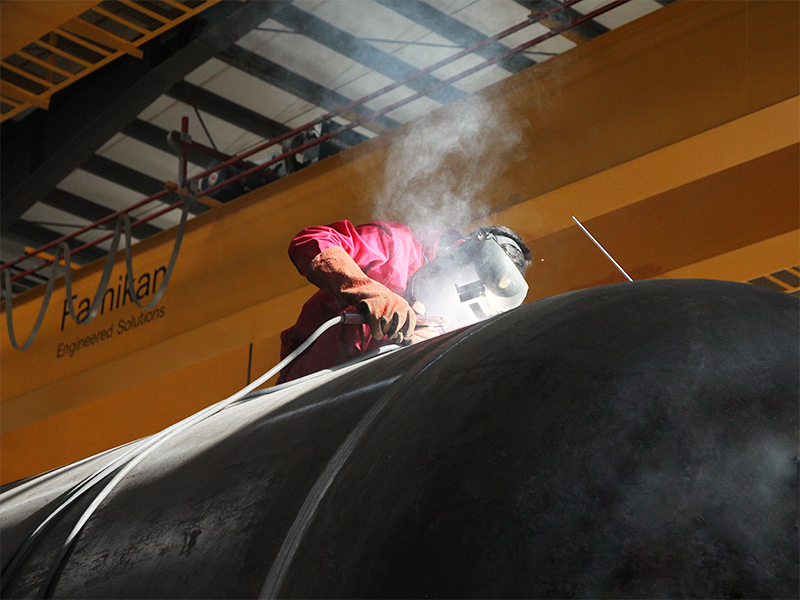
ASME Rules
Our expert pressure vessel fabrication department follows the ASME organization’s guideline which increases the service life of the made-to-order pressure vessels and equipment we produce. We follow the ASME in order to follow important safety design rules along with rules related to the construction, operation, testing and maintenance of pressure vessels, boilers, heat exchangers and other pressure systems.
We have invested in the most advanced welding equipment and welding techniques known in the industry. We comply with the highest welding-standards to ensure the quality of our equipment.
Our welding techniques include:
- Automatic Welding
- Submerged Arc Welding (SAW)
- Semi-Automatic Welding
- Flux-core Welding (FCAW)
- Manual Welding
- MIG Welding (GMAW)
- TIG Welding (GTAW)
- Stick Electrode Welding (SMAW)
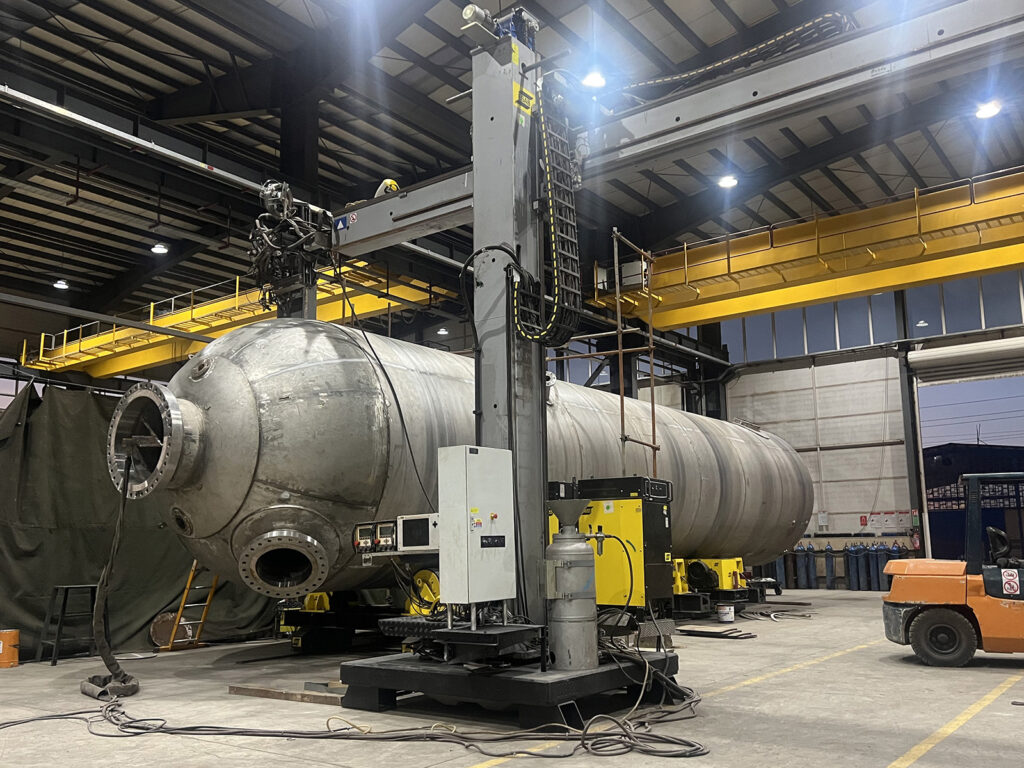
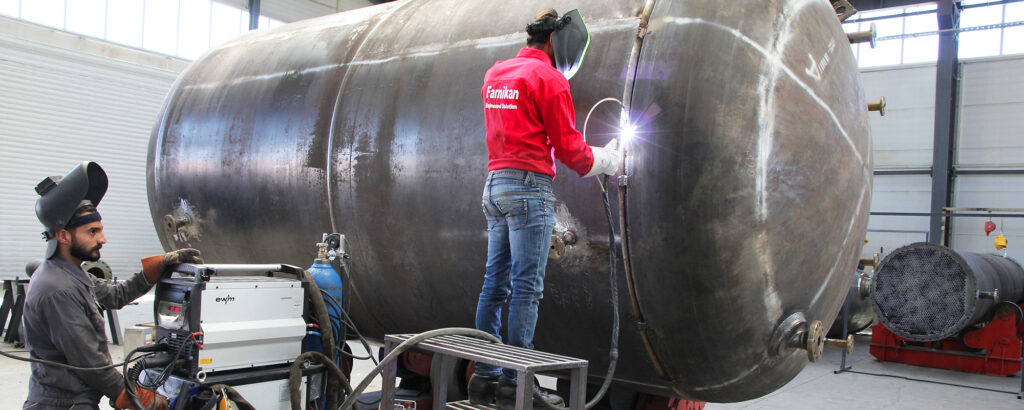
Advanced Fabrication Technology
We have invested in the most advanced welding equipment and welding techniques known in the industry. We comply with the highest welding standards to ensure the quality of our equipment.
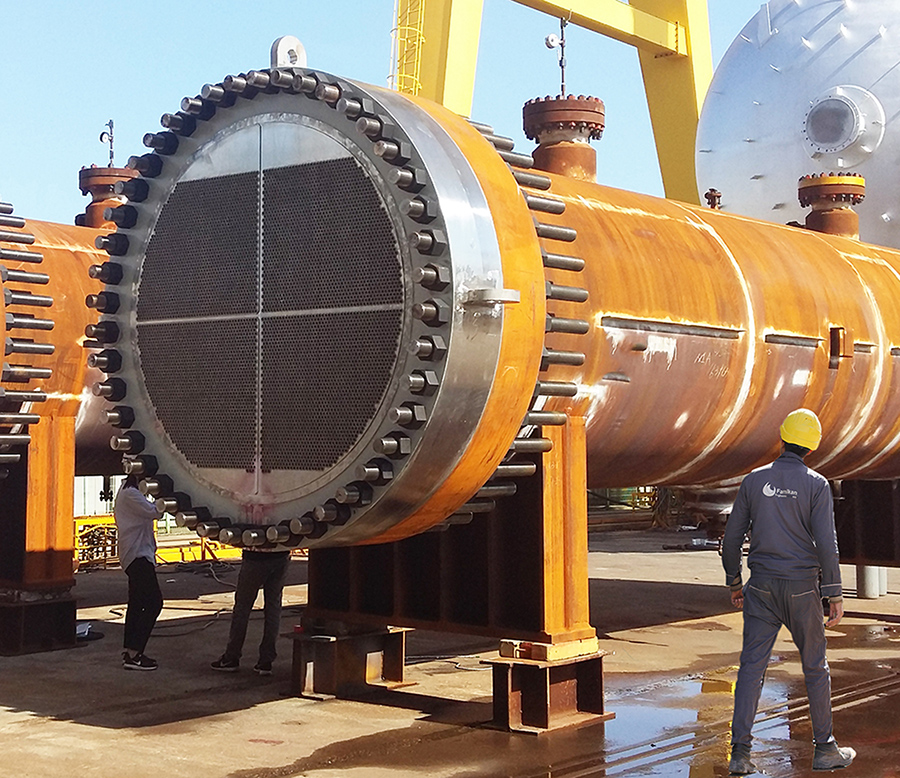
Material Selection
A variety of materials are used in the design of process equipment, including carbon steel, stainless steel, alloy steels, copper, bronze, brass, titanium and other various alloys. For example, regarding heat exchangers, the outer shell is made of a durable, high strength metal, such as graded carbon steel or stainless steel. Inner tubes require an effective combination of durability, corrosion resistance and thermal conductivity. All materials of construction is supplied according ASME BPVC, Sec II, and also specific requirements of client such as corrosion standards: SCC, HIC and NACE. For all cases we provide our client with the original or true copy of mill test certificates showing material specifications, chemical & mechanical properties and also any type of standard lab tests required by our client. These documents will be submitted at final stage of project and can be traced by client at any stage of fabrication according to inspection test plan of project.
- Carbon Steel
- Stainless Steel
- Non-ferrous alloy,
- Inconel, nickel, Hastelloy
- Titanium
Non Destructive Test
All ASME pressure vessels are subjected to rigorous testing during the fabrication phase.
They are visually examined by our inspectors and also by an authorized third party inspection company subjected to below test according to Inspection Test Plan which is mutually agreed by us and our clients:
- Radiography (RT)
- Ultrasonic (UT)
- Phased Array Ultrasonic Test (PAUT)
- Magnetic Particle Testing (MT)
- Liquid Penetrant Testing (PT)
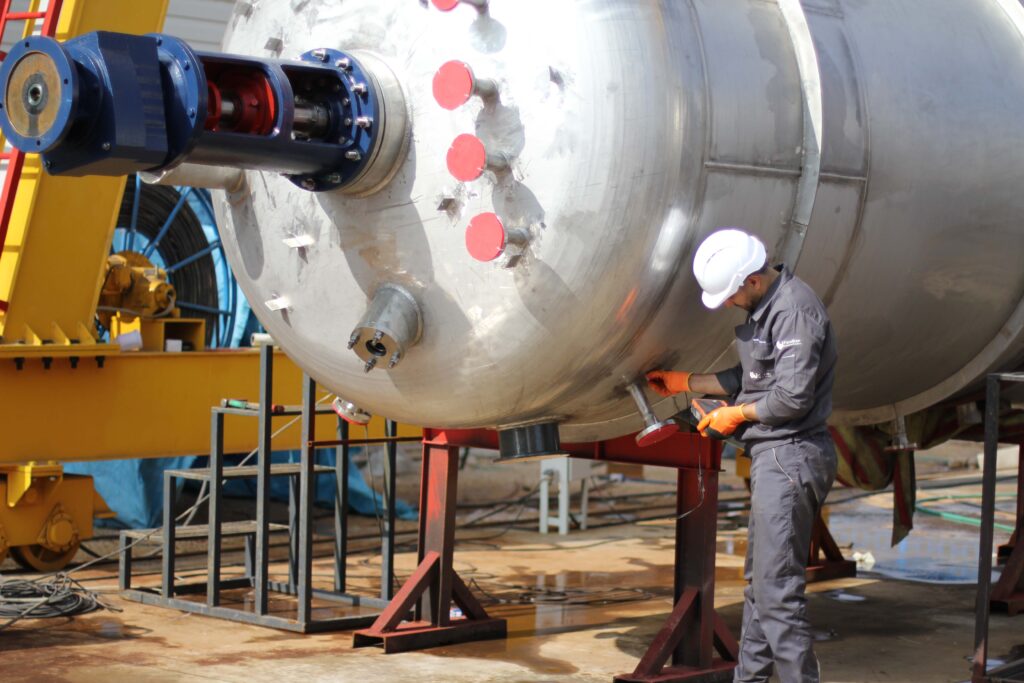