Home / Process Reactors
Reactor
As the name implies, they are to facilitate desired reaction of liquid / vapor which are typically equipment:
- Heavy Wall Reactor
- Reactor with Special Internals
- Catalyst Reactor
- Agitator Reactor
Our ability to manufacture thick walled pressure vessels requires high level of capabilities including design capabilities, materials knowledge, welding engineering, intelligent fabrication sequences, materials handling, project management, scheduling logistics and quality assurance. Through a strong commitment to continuous upgrading of facilities, and investment in new technologies and people, Farnikan rises to the challenge with a “world class” facility with very unique capabilities. We have largely improved our skills in the fabrication of process equipments for heavy industries.
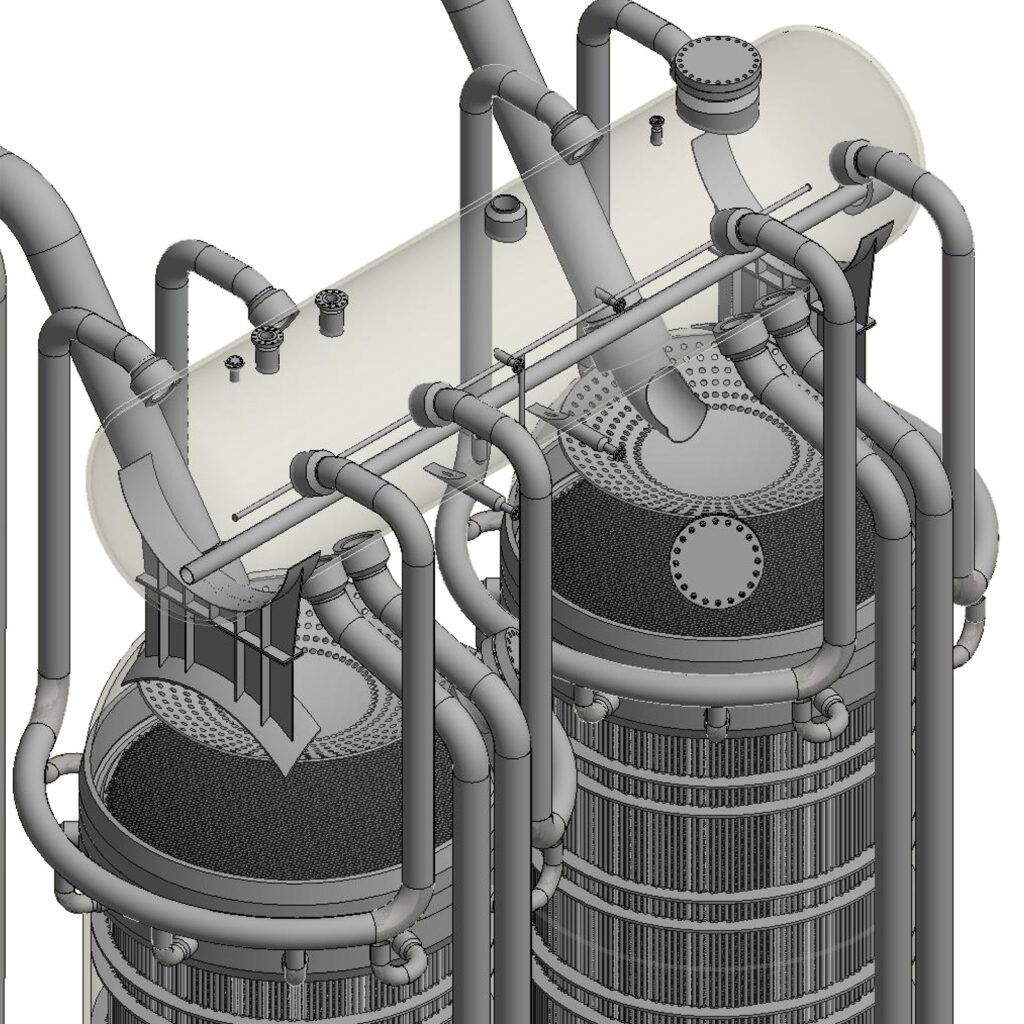
DESIGN & ENGINEERING
We provide our designs with in-house engineering and extensive experience in design, analysis of Reactors used in refineries, chemical and power plants and other processing facilities..
By using general purpose softwares as well as international code based softwares, FEA and also hand calculations in accordance with all of the pressure vessel codes, Farnikan is able to mechanical design and 3D modeling and 2D drafting of Reactor equipment
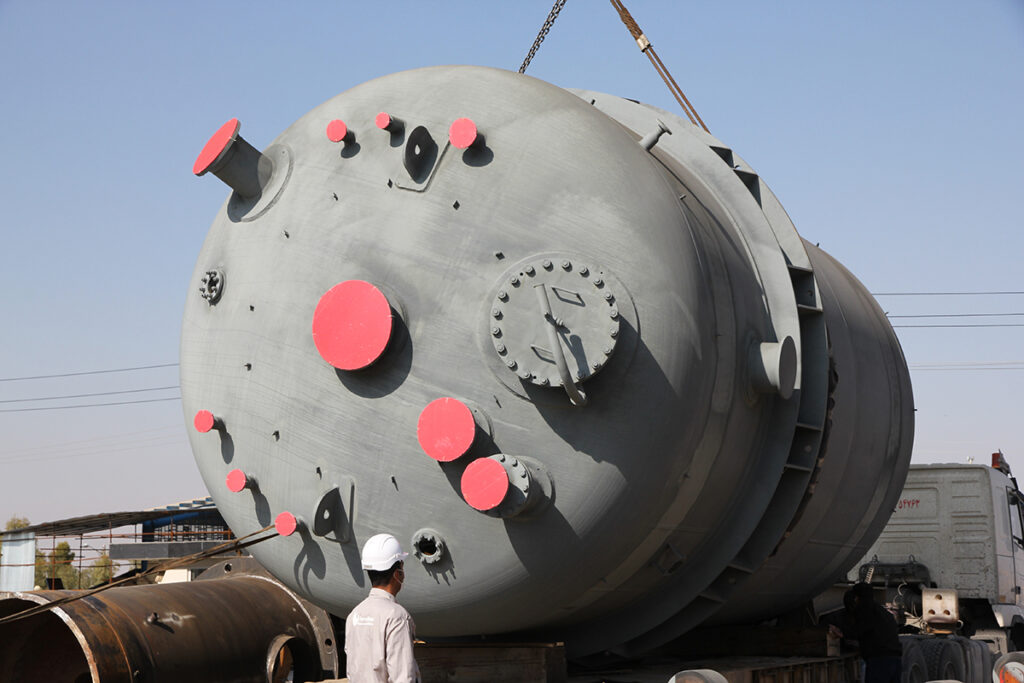
SPECIAL MATERIAL
Heavy walled Reactors are being manufactured using conventional Cr-Mo & advanced Cr-Mo-V base material. The characteristics of advanced Cr-Mo steel, such as higher resistance to hydrogen atmosphere, higher creep rupture strength and lower susceptibility to long term degradation were verified through enough experiences based on the latest technology of manufacturing and operation of the vessels.
The vessel material selection is based on
(a) high temperature creep resistance- Cr-Mo / Cr-Mo-V steel
(b) corrosion resistance to hydrogen atmosphere through use of SS 347 cladding / overlay on inside surface.
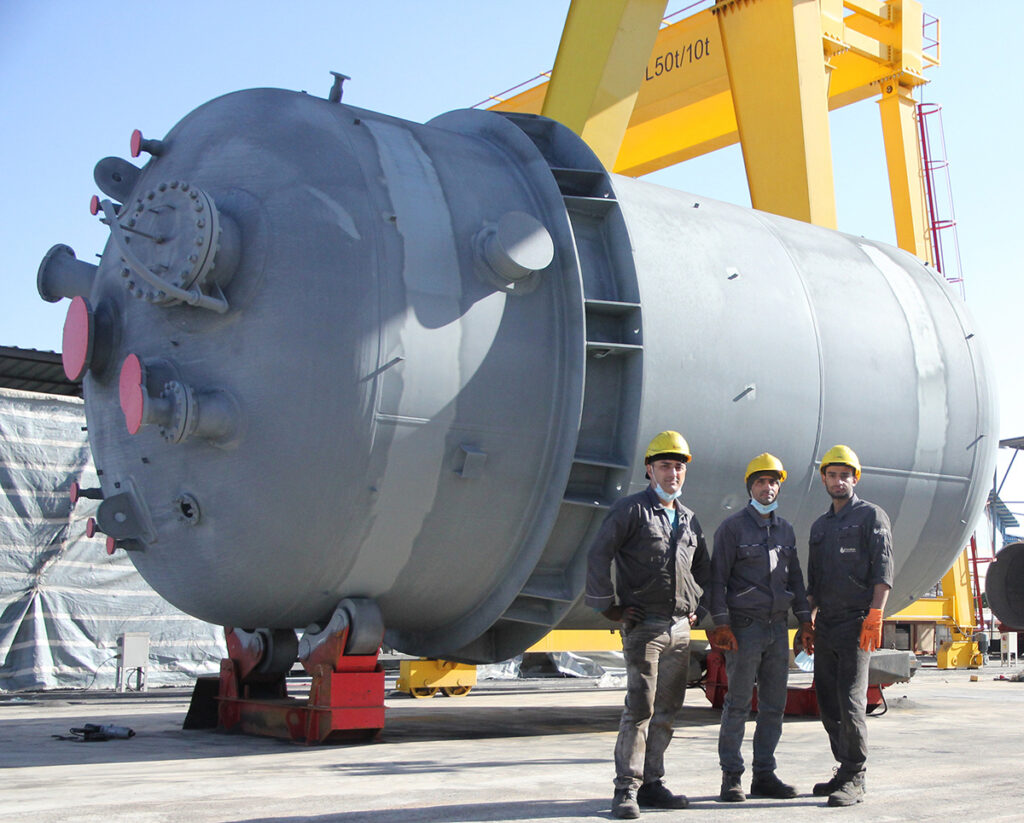
Special Fabrication Facilites
The complexities of the equipment and the design requirements provides lots of challenges in design and engineering, manufacturing technologies and execution levels. Some of the critical manufacturing technologies which we have developed are:
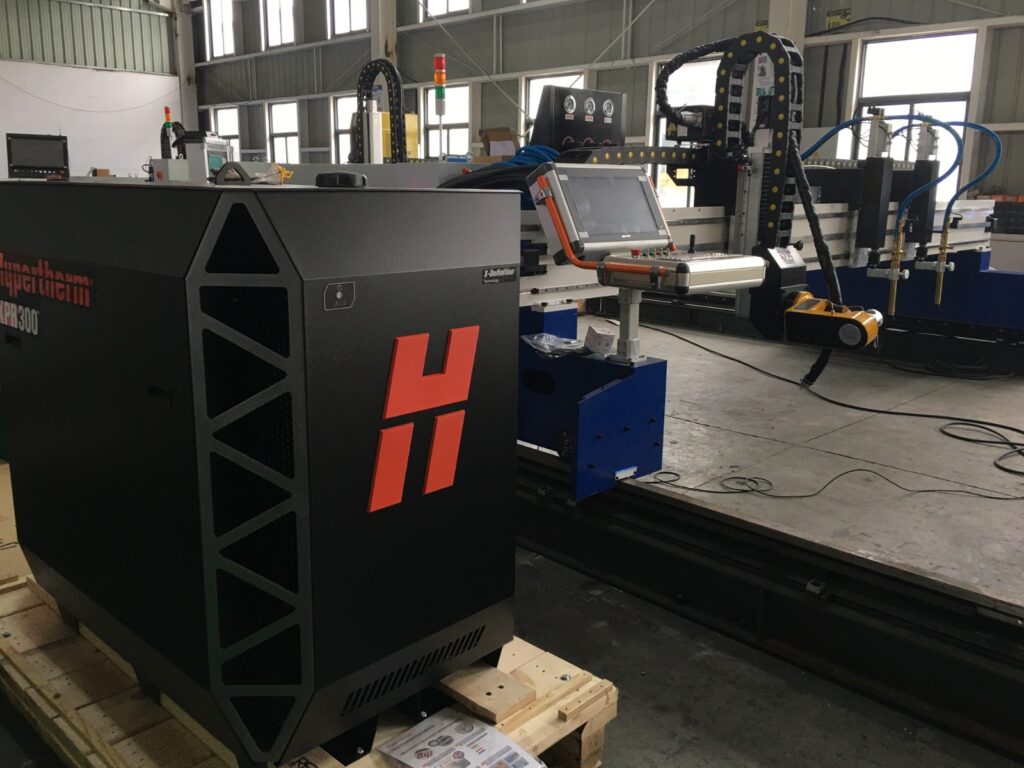
5 AXIS CNC CUTTING
Thick wall Oxy-fuel / Plasma cutting stations and Special 5 axis CNC cutting machine equipped with the most advanced plasma power-sources
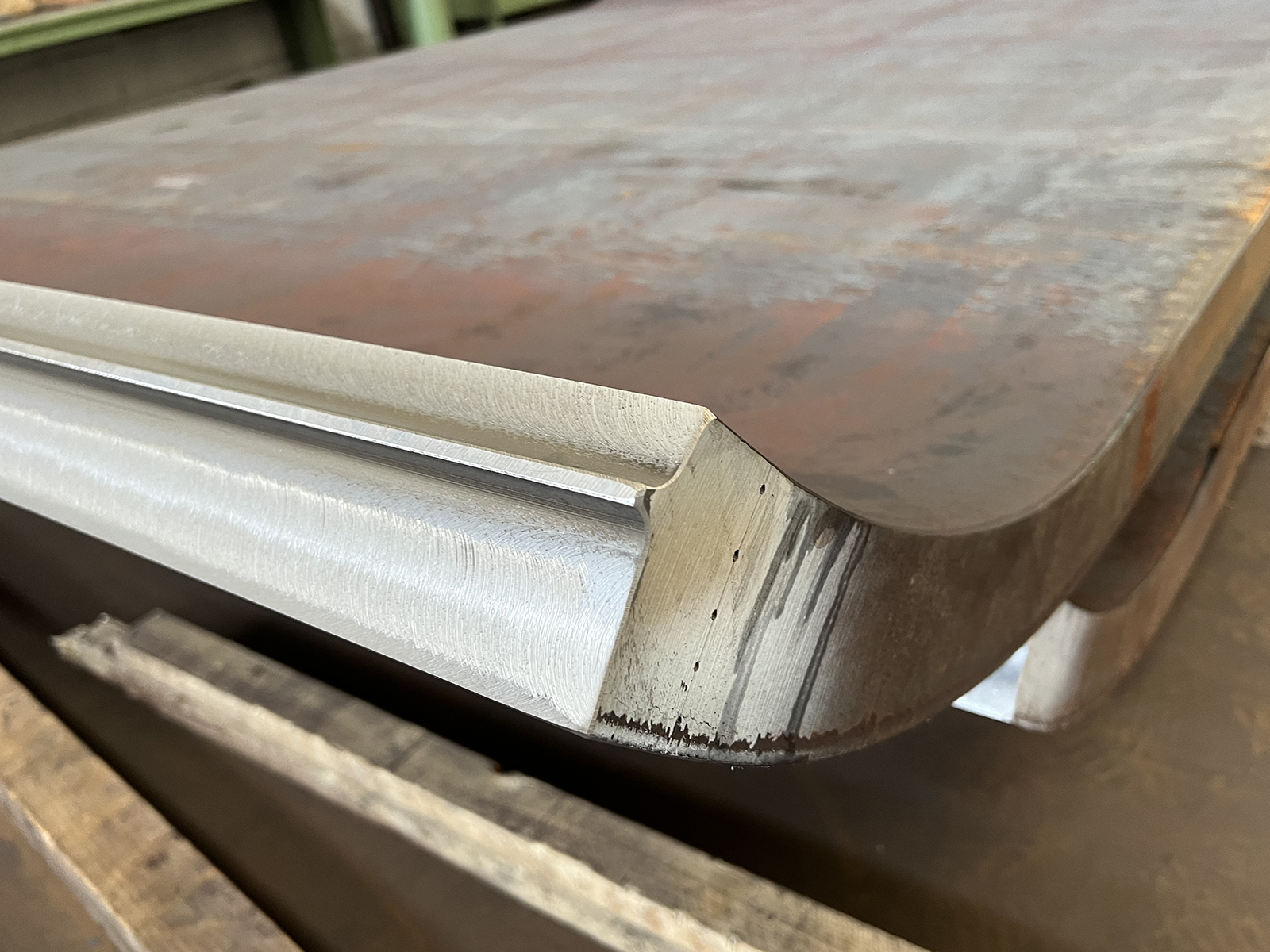
EDGE PREPARATION
Mechanized edge milling station to have high quality bevelling details up to 200 mm thickness.
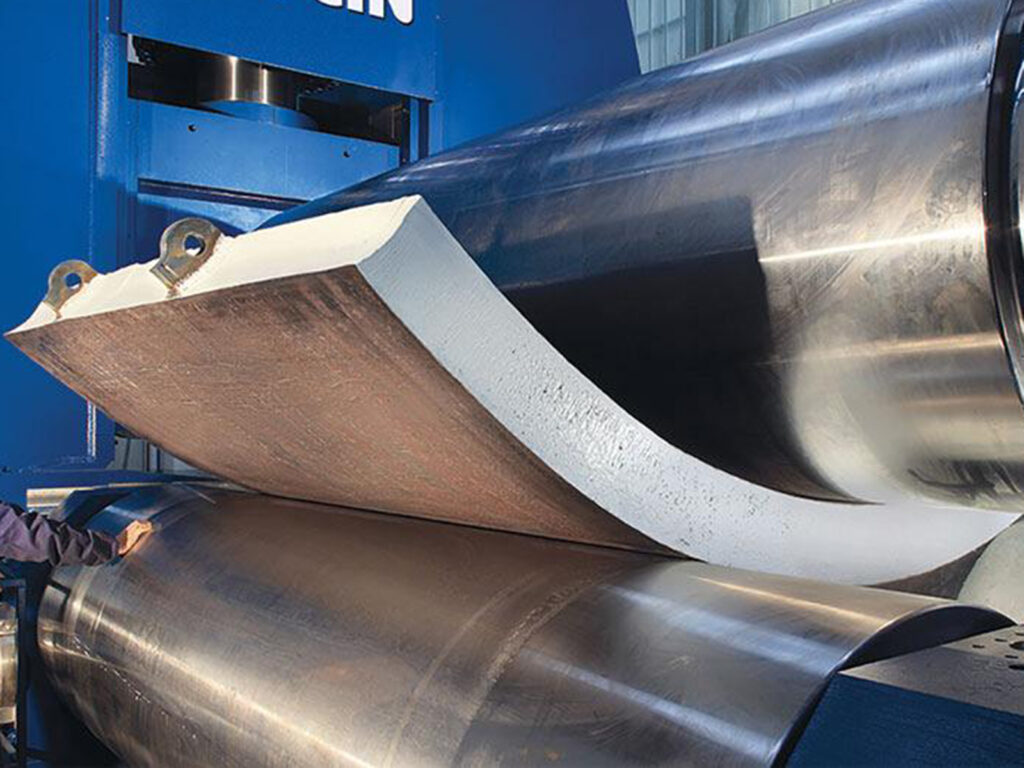
HEAVY DUTY ROLL BENDING
Heavy Duty roll bending machine with capacity up to 180 mm thk (Cold Forming)
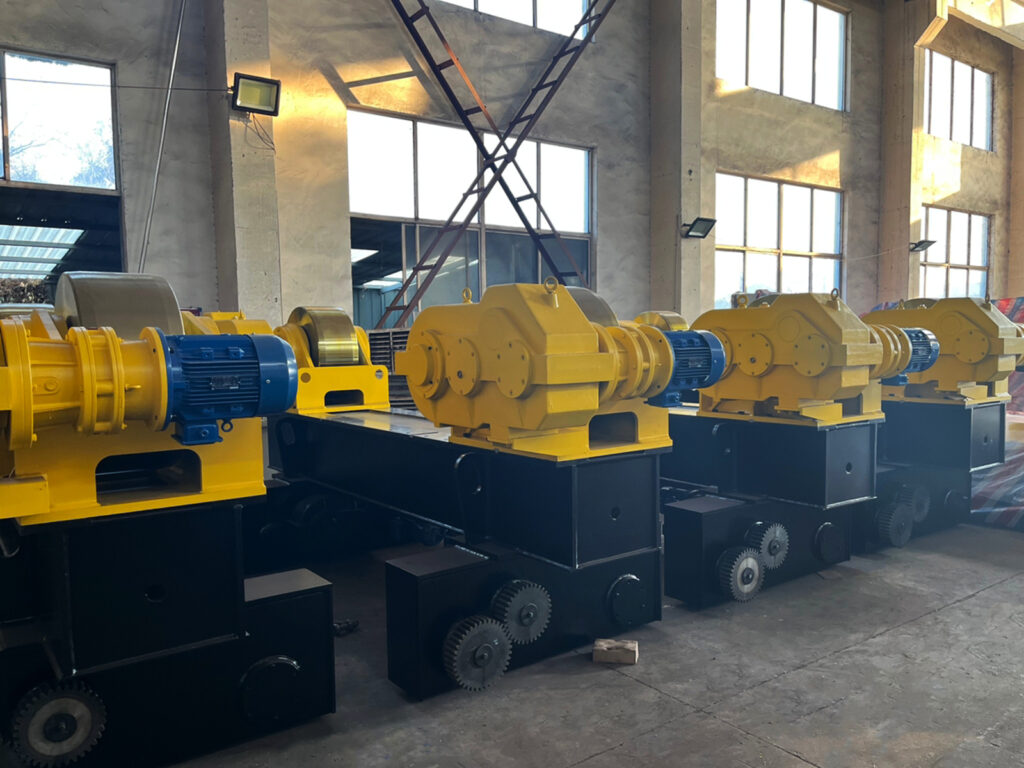
HEAVY DUTY FITTUP STATION
Several stations of Narrow Gap Submerged Arc Welding (NG-SAW) for Longitudinal and Circumferential seams of Shell courses by DC-AC Tandem SAW
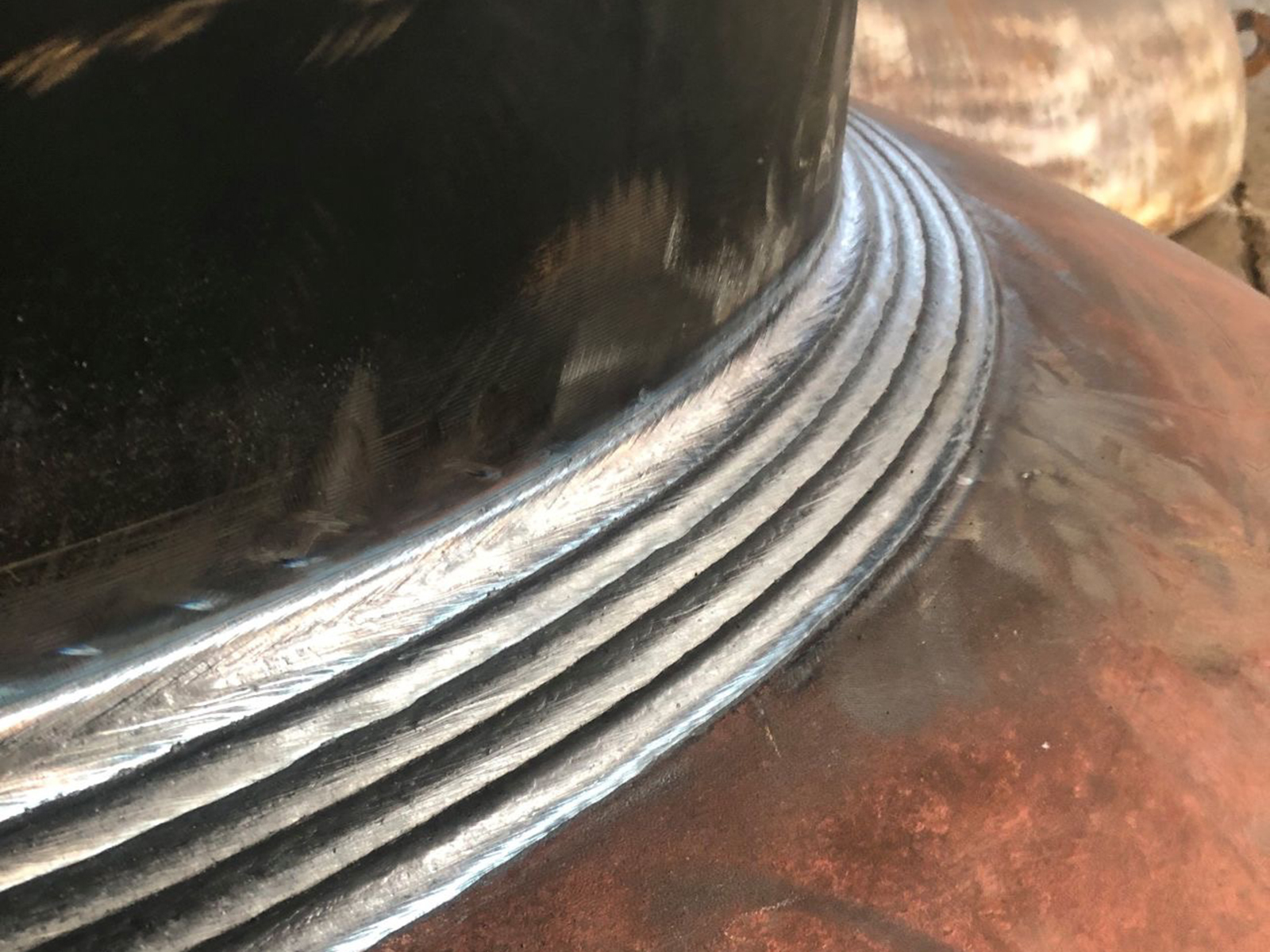
ORBITAL SAW NOZZLE WELDER
Mechanized Nozzle to Shell / Head butt joints using Orbital SAW nozzle welder
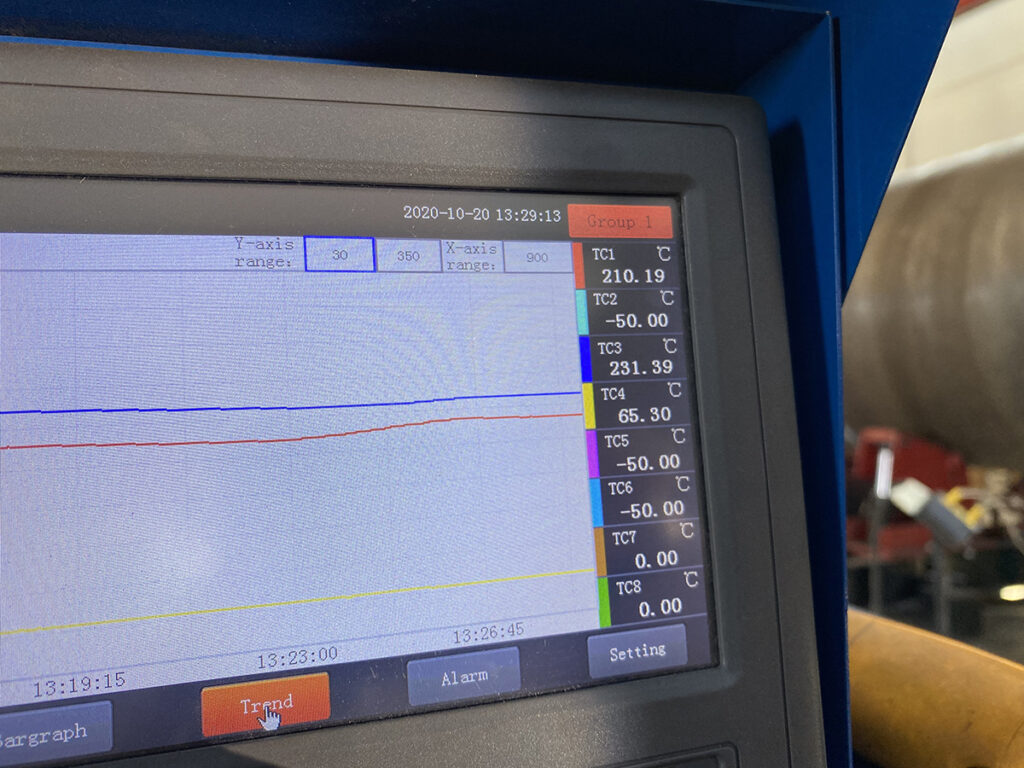
PRE-HEAT & DHT / PWHT
Development of Local heat preheat / DHT / Local PWHT treatment during and just after welding.
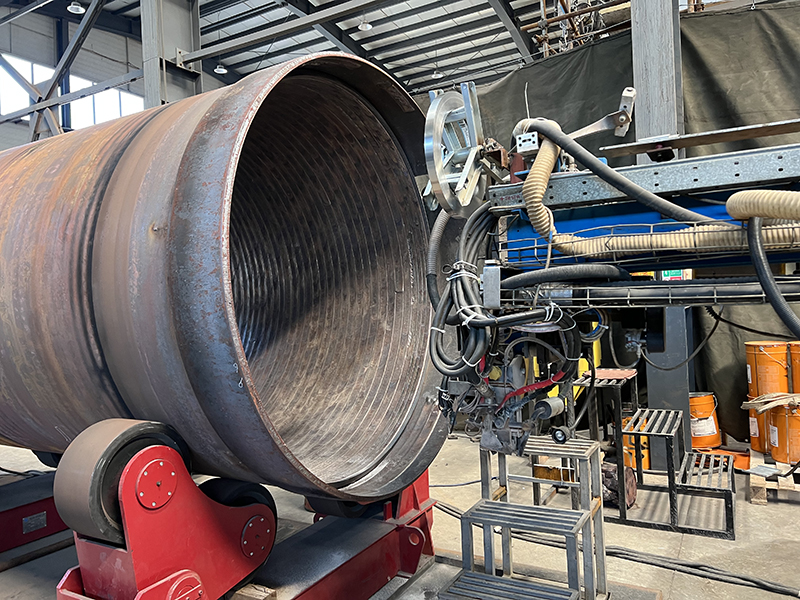
ESW STRIP CLADDING
Farnikan uses the latest ESAB ESW / LINCOLN ESW strip cladding technology to perform high quality and efficient weld overlay wide strip cladding for internal surface of process rectors and pressure vessels.
Depending on size and service we are able to make cladding by strips: 30 x 0.5 mm / 60 x 0.5 mm / 90 x 0.5 mm.
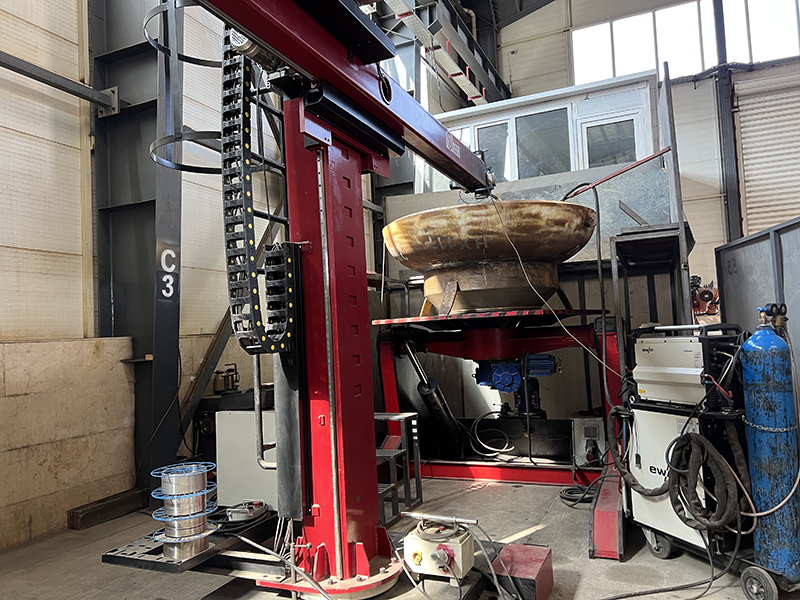
FLANGE CLADDING
We use hot-wire tig welding tools for cladding inside of pipes as flanges. Cladding flanges make use of a weld overlay cladding technology process that builds up the corrosion resistant alloy (CRA) layer on the welded parts of pipes and other piping components (e.g., valves, flanges). It protects the piping system’s integrity, and provides a low cost and long-term solution.
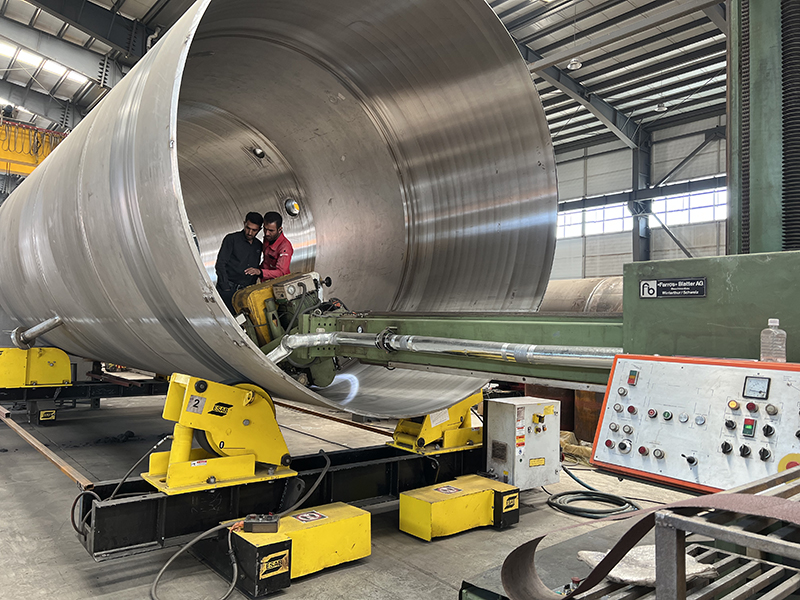
SURFACE POLISHING
We use one of the most modern mechanical polishing tools for internal surface polishing of those applications which needs certain level of finishing texture. Mechanical polishing is performed in steps with progressively finer abrasives until the desired smoothness is achieved. The precision polishing process removes material and plastically deforms the surface while it alters the macroscopic and microscopic surface texture.
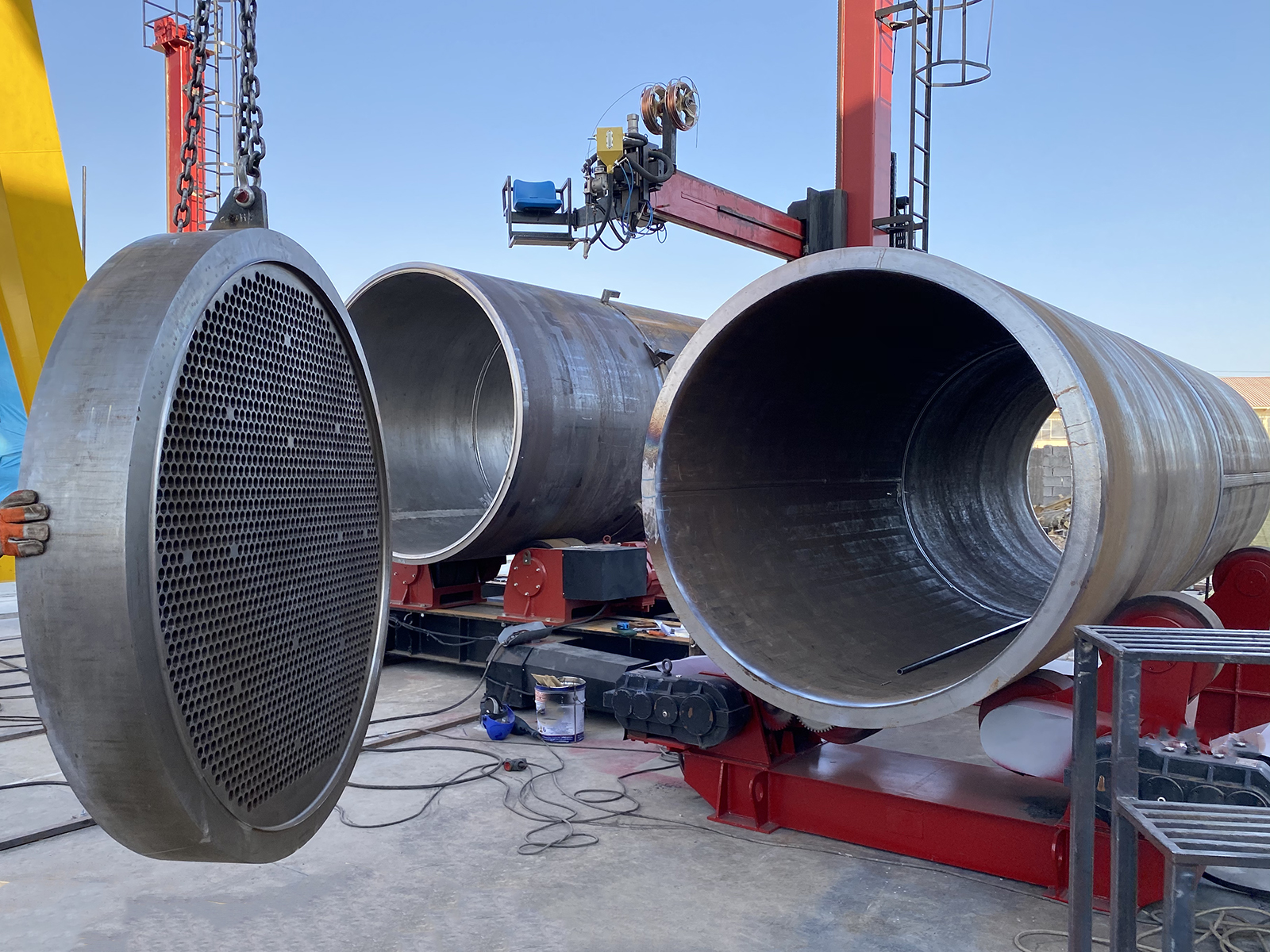
NARROW GAP SAW
Several stations of Narrow Gap Submerged Arc Welding (NG-SAW) for Longitudinal and Circumferential seams of Shell courses by DC-AC Tandem SAW
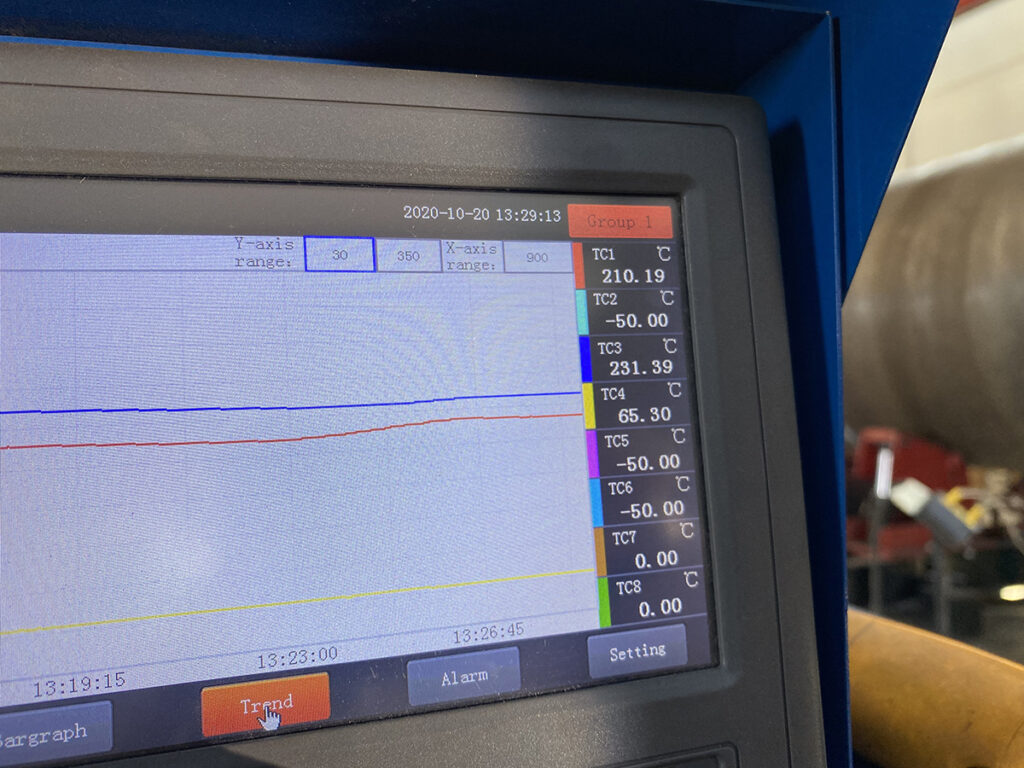
HEAT TREATMENT
Development of Local heat preheat / post weld head treatment as well as modular furnace according to desired size of vessels
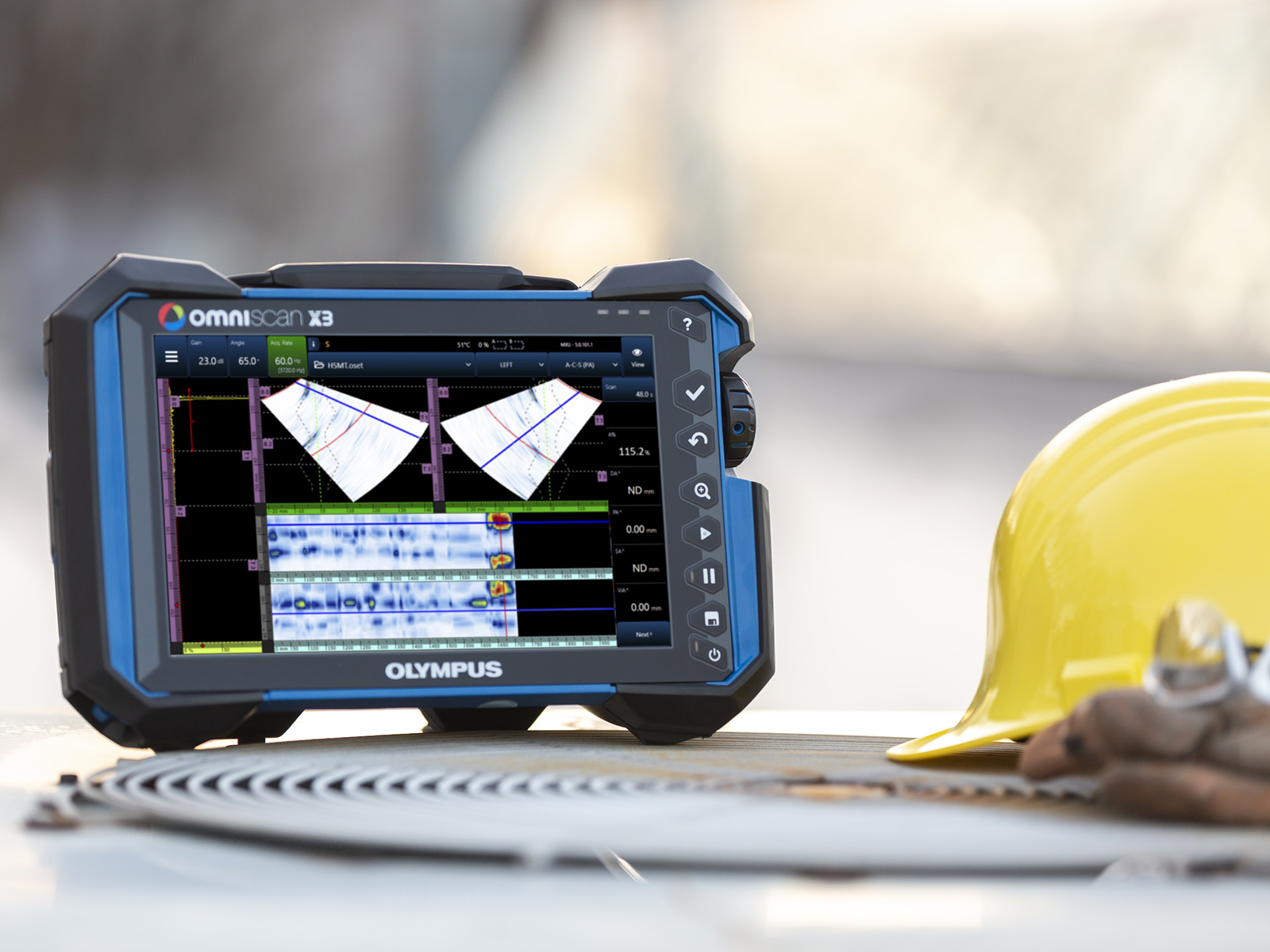
PAUT
NDE techniques are TOFD, CB-Scan, Phased Array in accordance with ASME C.C. 2235 instead of RT for heavy wall components.
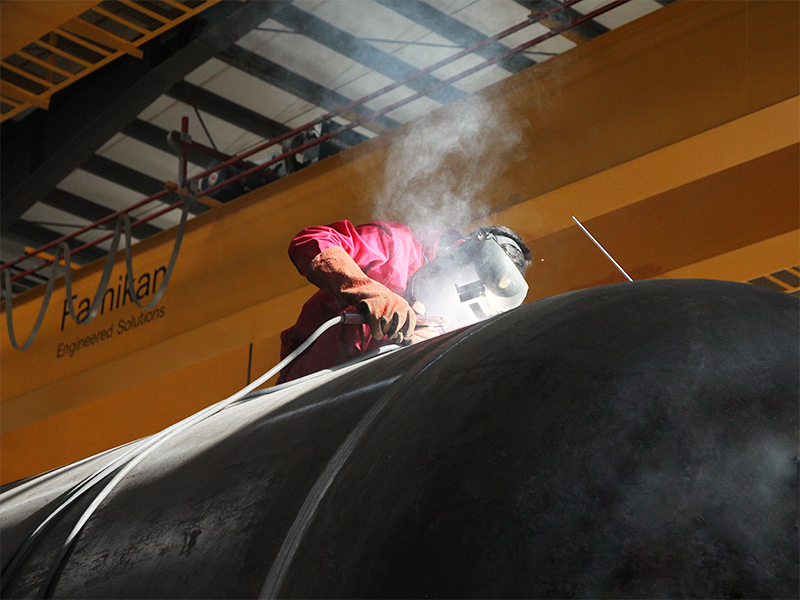
ASME Rules
Our expert pressure vessel fabrication department follows the ASME organization’s guideline which increases the service life of the made-to-order pressure vessels and equipment we produce. We follow the ASME in order to follow important safety design rules along with rules related to the construction, operation, testing and maintenance of pressure vessels, boilers, heat exchangers and other pressure systems.
We have invested in the most advanced welding equipment and welding techniques known in the industry. We comply with the highest welding-standards to ensure the quality of our equipment.
Our welding techniques include:
- Automatic Welding
- Submerged Arc Welding (SAW)
- Semi-Automatic Welding
- Flux-core Welding (FCAW)
- Manual Welding
- MIG Welding (GMAW)
- TIG Welding (GTAW)
- Stick Electrode Welding (SMAW)
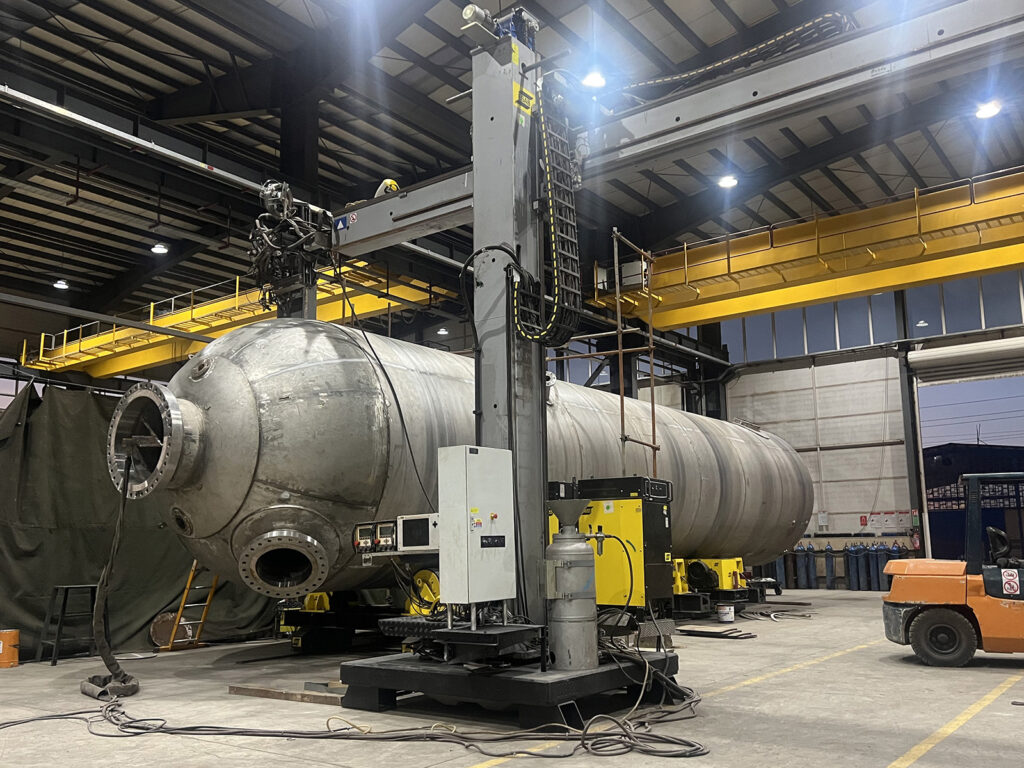
We use custom designed welding machines with special Tandem / Twin welding heads
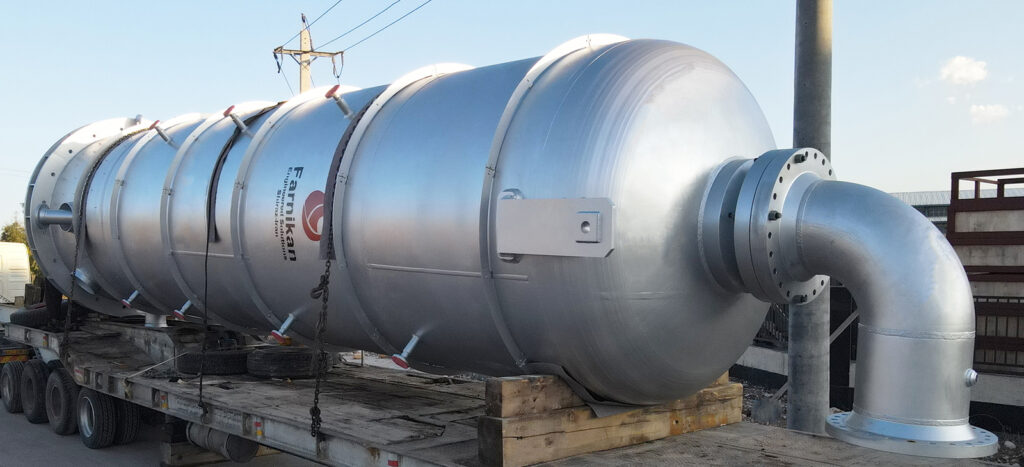
Application of Process Reactors
Non Destructive Test
All ASME pressure vessels are subjected to rigorous testing during the fabrication phase.
They are visually examined by our inspectors and also by an authorized third party inspection company subjected to below test according to Inspection Test Plan which is mutually agreed by us and our clients:
- Radiography (RT)
- Ultrasonic (UT)
- Magnetic Particle Testing
- Liquid Penetrant Testing
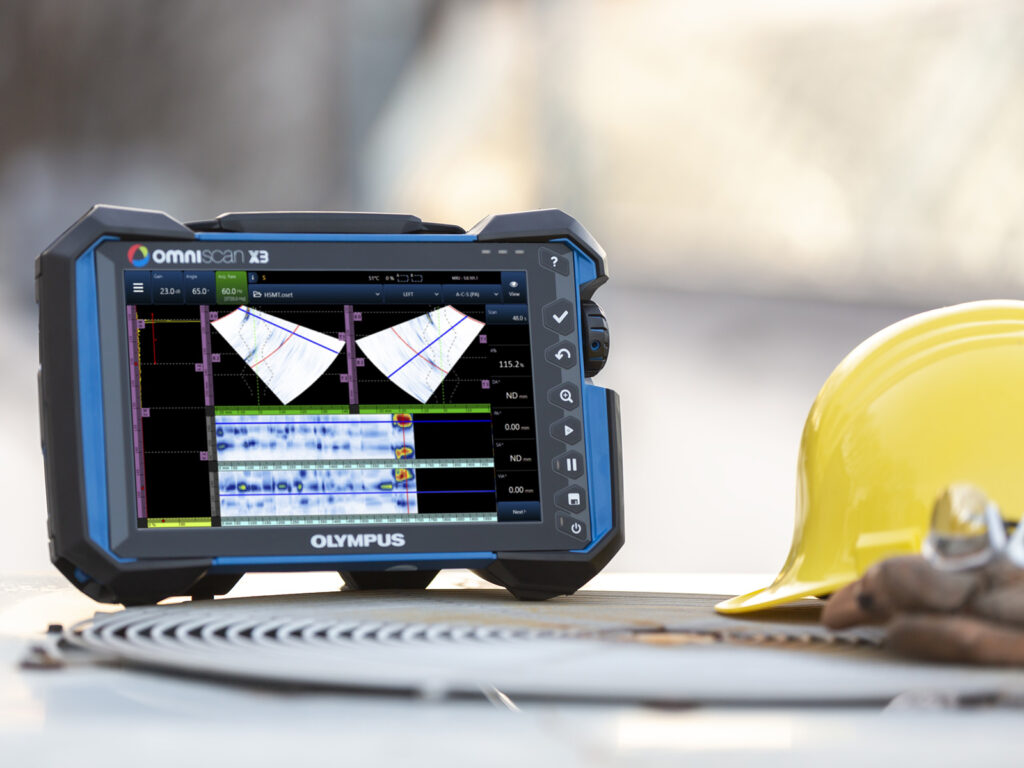
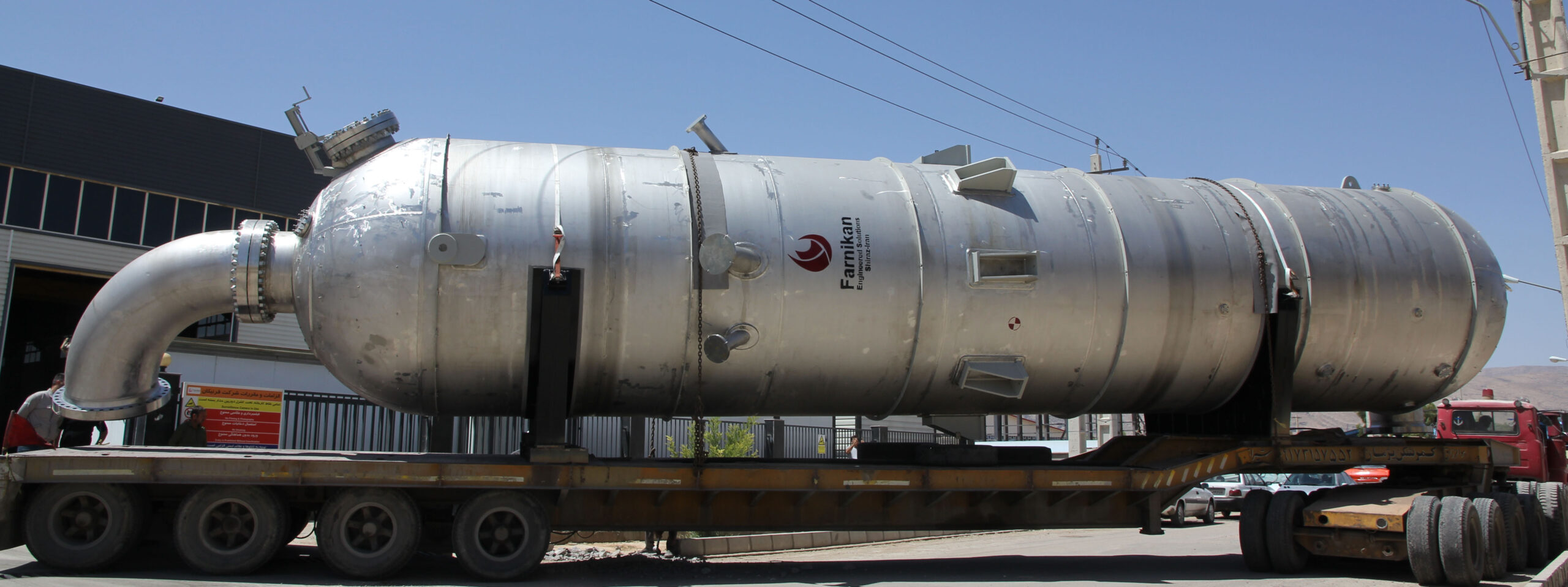
Heat Transfer Principle
Process Criteria
How does an Chemical Reactor work?
A reactor is a process vessel design to add chemicals and conduct chemical reactions. The chemical reactor consists of different parts Chemical reactors are designed to give maximum yield in a chemical reaction. Different types of reactions are being carried out in chemical reactors.