Home / Plate Heat Exchangers
Plate Heat Exchangers
- Gasketed Type (Plate & Frame)
- Semi-Welded Type (Plate & Frame)
- Welded Plate & Frame
- All-Welded Block Type
- All-Welded Plate & Shell
- Spiral PHE
A plate exchanger consists of a series of parallel plates that are placed one above the other so as to allow the formation of a series of channels for fluids to flow between them. The space between two adjacent plates forms the channel in which the fluid flows. Inlet and outlet holes at the corners of the plates allow hot and cold fluids through alternating channels in the exchanger so that a plate is always in contact on one side with the hot fluid and the other with the cold. Generally, these plates are corrugated in order to increase the turbulence, the thermal exchange surface and to provide mechanical rigidity to the exchanger. Corrugation is achieved by cold forging of sheet metal with thicknesses of 0.3 mm to 1 mm.
Plate Heat Exchangers serve many different purposes and are used in multiple industries:
- Food & Beverage
- Petroleum / Chemical Processing (Refinery, Oil & Gas, Dehydration / Desolving, Desulphurization)
- Hydrocarbon Processing (Methanol, Polyethylene, Polypropylene, etc.)
- Petrochemical Plants
- Refrigeration
- Pharmaceutical
- Industrial (Mining, Automotive, etc.)
- HVAC – Heating / Air Conditioning, Power and Energy production
- Marine & Shipbuilding
- Steel Mills and Metal Works
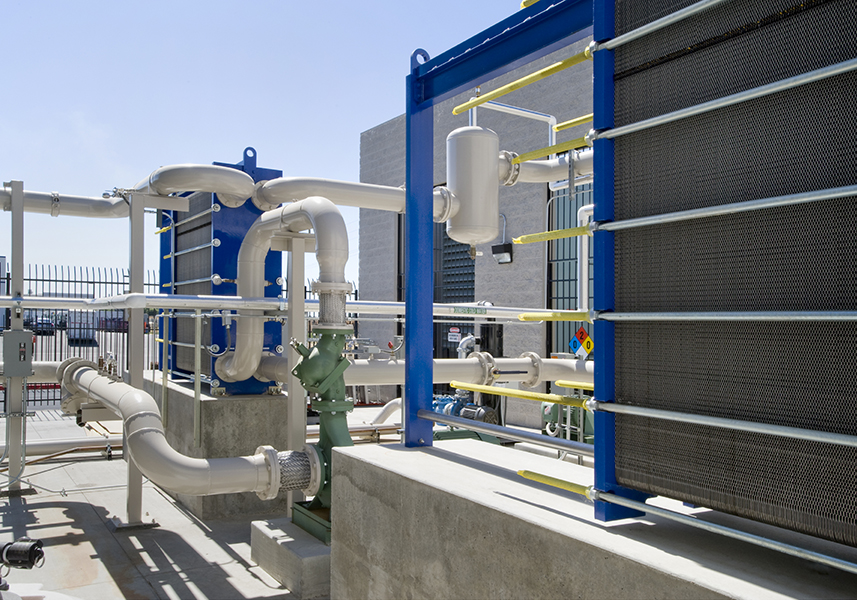
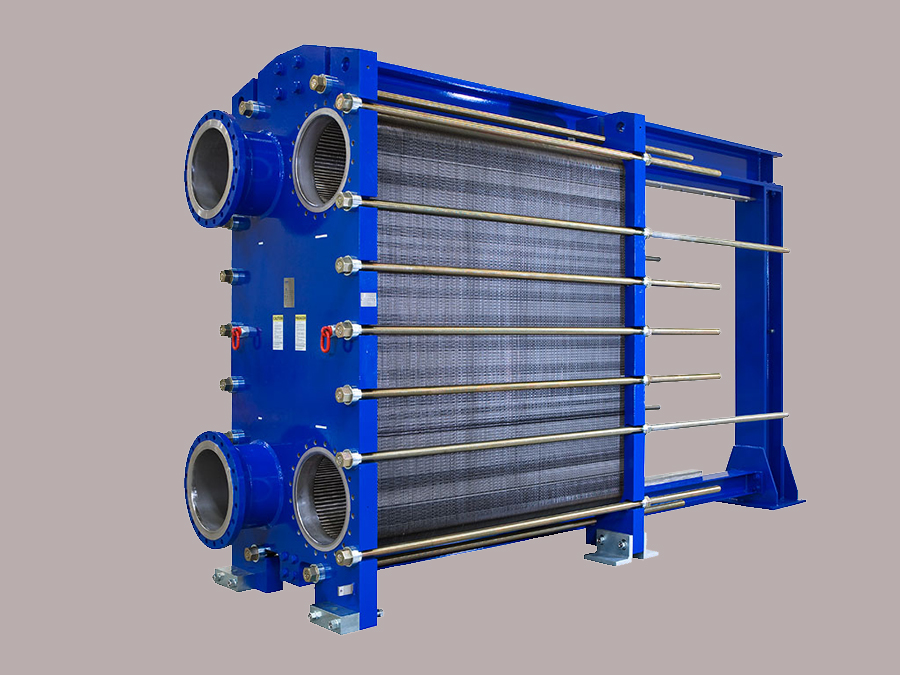
Gasketed (Plate & Frame)
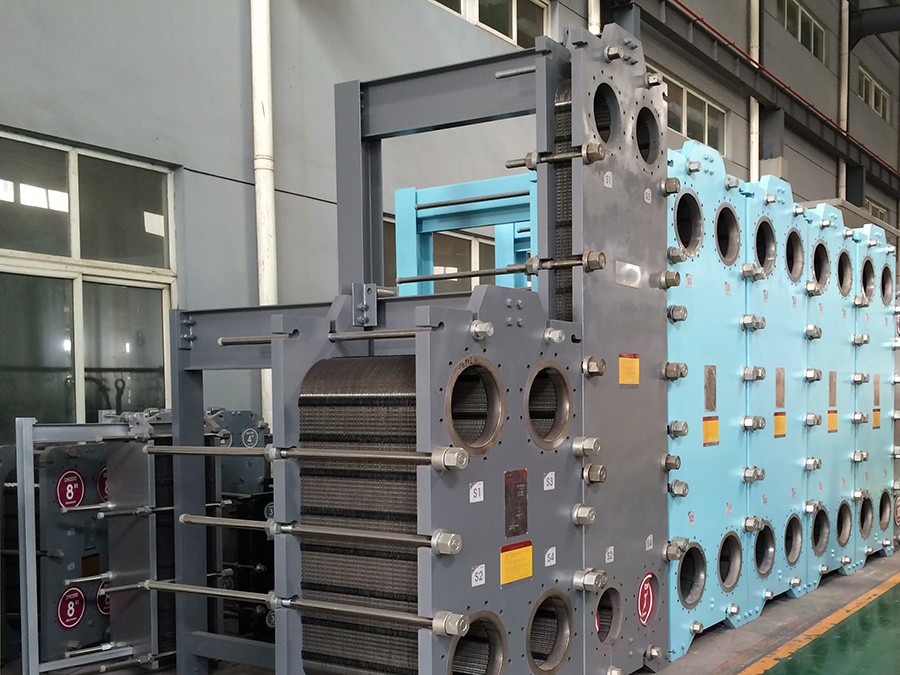
Semi Welded (Plate & Frame)
By welding heat exchanger plates in pairs, to make what are commercially called twin plates or semi-welded Plate Heat Exchangers will be created. With a light weight and applicability for heavy duties semi welded Exchangers will highlighted among other types. Semi-welded gasketed plate heat exchangers are used when gaskets are not suitable as one of the process media. Semi-welded can also take a higher design pressure compared to fully gasketed plate-and-frame heat exchangers. In the Semi-welded heat exchanger the refrigerant flows in laser-welded, sealed plate channels, and in the opposite channel the liquid brine flows in gasketed channels.
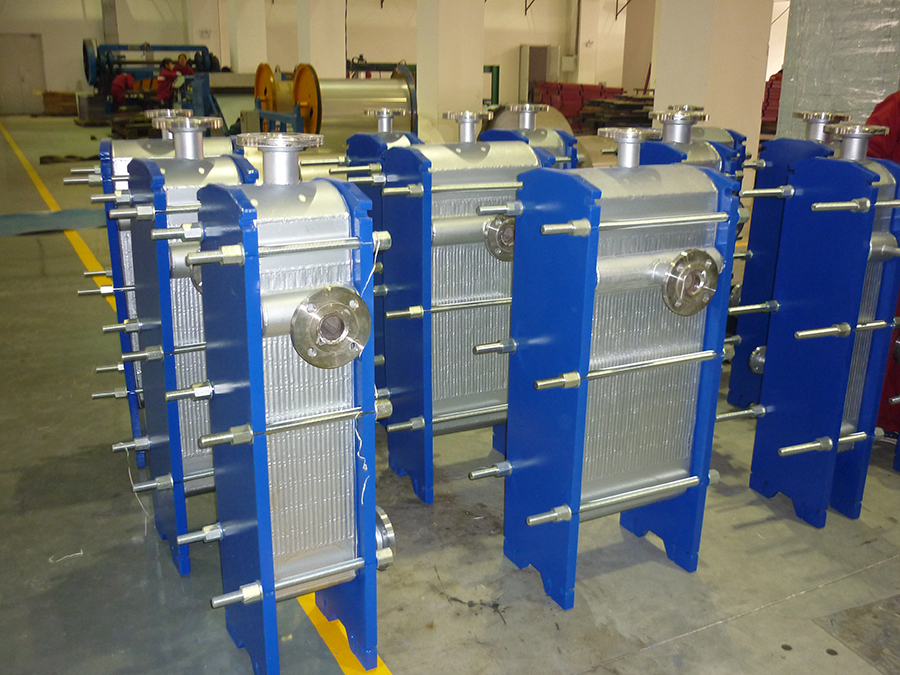
Fully Welded (Plate & Frame)
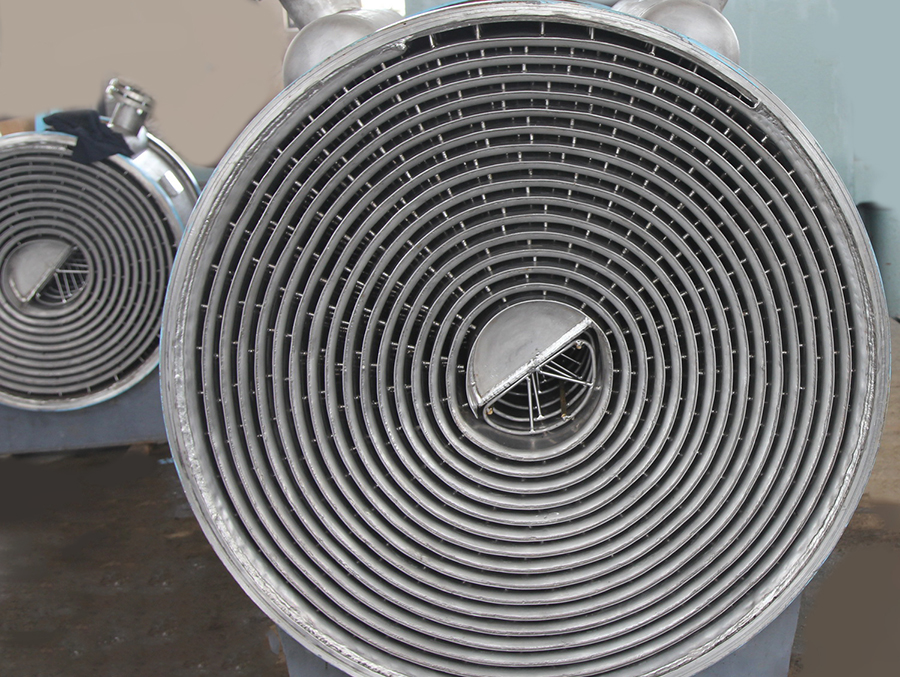
Spiral
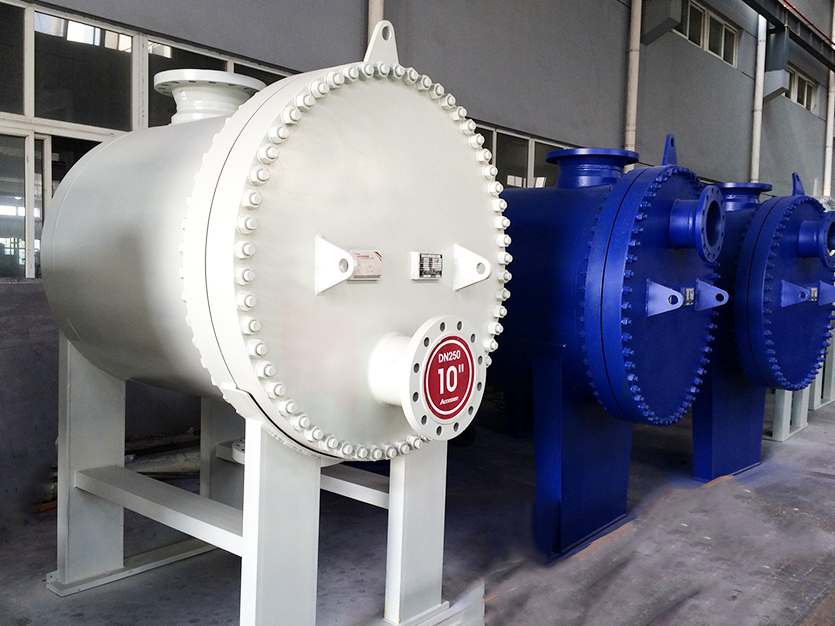
Shell & Plate
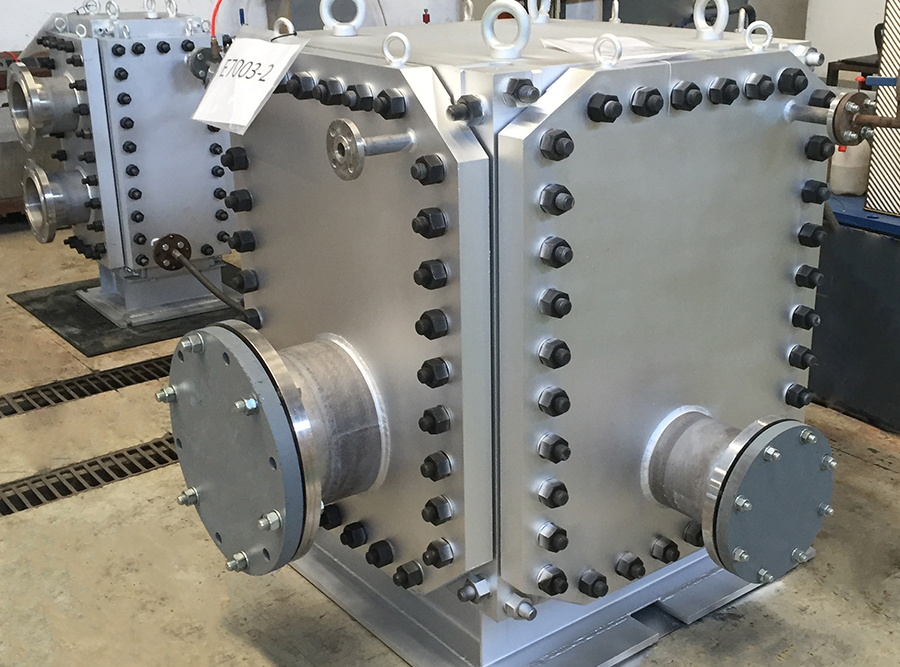
Fully Welded Block Type
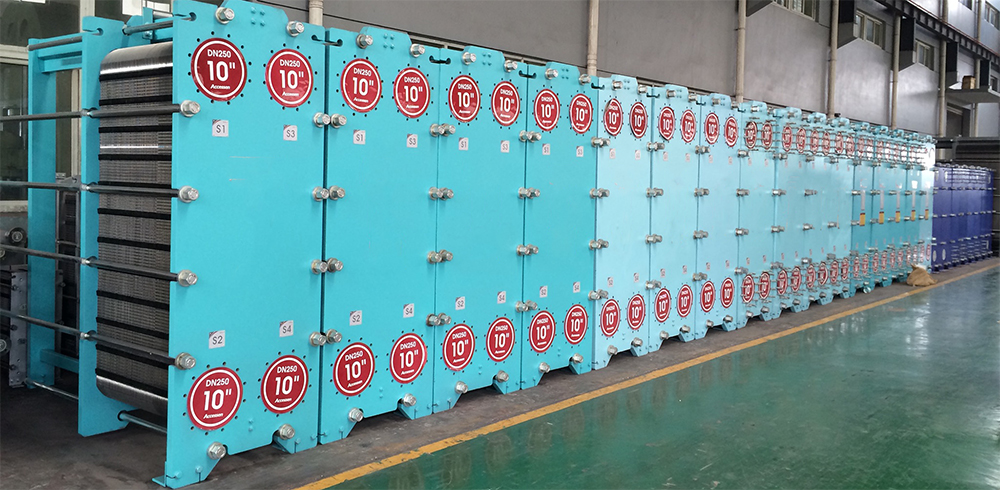
Redesign and Replacement of PHE units
We have enough technical knowledge and capability to offer our clients with the replacement of Plate Heat Exchanger Units which are not going to be supported by the previous manufacturers anymore. In this case we design new equipment and ensures the plate heat exchanger configuration meets current process requirements. This activity may include updates with new technology and material upgrades as well as increase in performance and reduction in maintenance.
Our optimisation plan includes:
- Optimize for greater Energy Saving
- Optimize for increased Performance & Capacity
- Optimize for Reduction of Maintenance
- Optimize for Materials in sever conditions
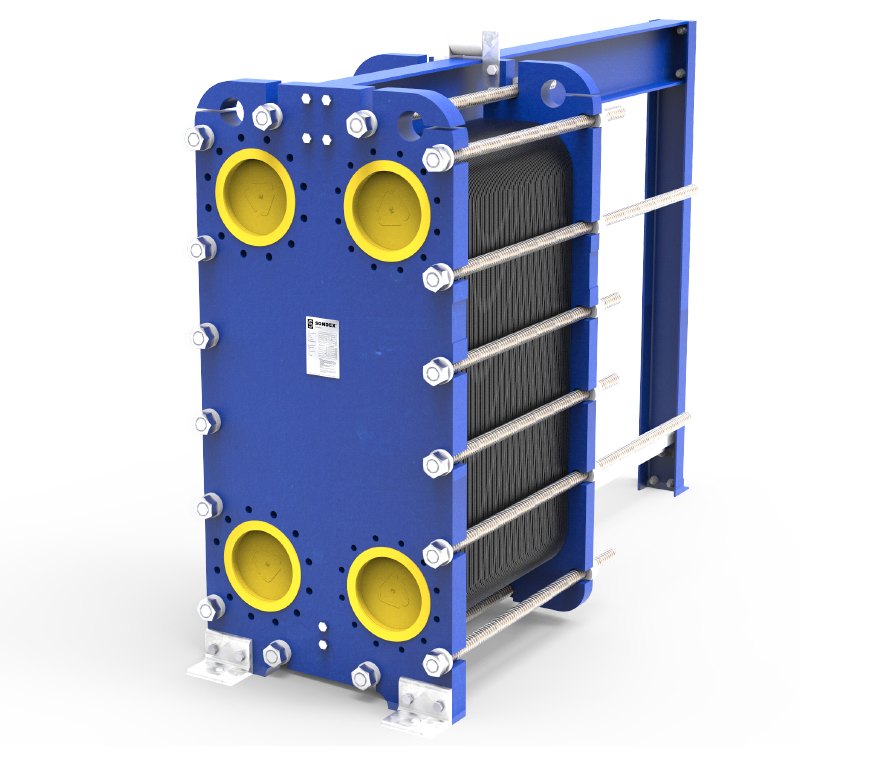
Supply of Spare Parts:
Our procurement department is available to support the clients with supply of spare plates & gaskets and other related parts and accessories for well-known manufactures in the soonest delivery. We are able to supply most of models for below brands:
- Alfalaval
- Sondex
- APV
- Tranter
- Hisaka
- GEA
Overseas Paetners
Plate heat exchangers consist of thin plates joined together, with a small amount of space between each plate, typically maintained by a small rubber gasket. The surface area is large, and the corners of each rectangular plate feature an opening through which fluid can flow between plates, extracting heat from the plates as it flows. The fluid channels themselves alternate hot and cold fluids, meaning that heat exchangers can effectively cool as well as heat fluid—they are often used in refrigeration applications. Because plate heat exchangers have such a large surface area.
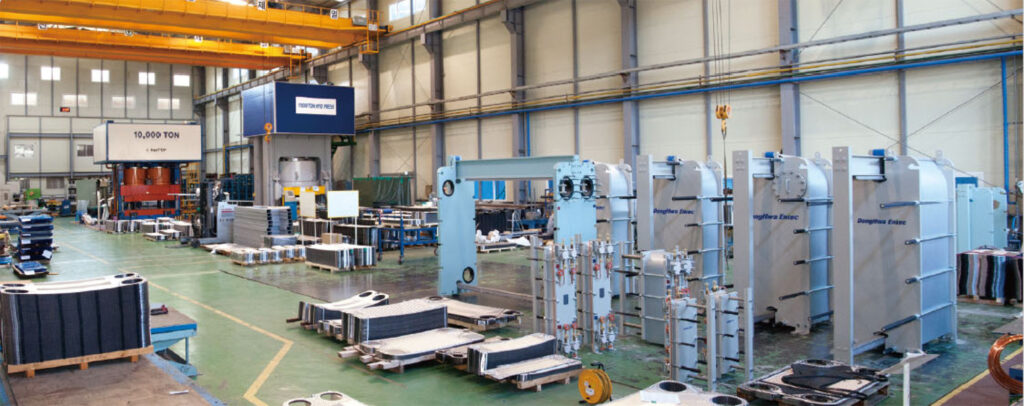

Heat Transfer Principle
Process Criteria
How does a Plate Heat Exchanger work?
Plate heat exchangers consist of thin plates joined together, with a small amount of space between each plate, typically maintained by a small rubber gasket. The surface area is large, and the corners of each rectangular plate feature an opening through which fluid can flow between plates, extracting heat from the plates as it flows. The fluid channels themselves alternate hot and cold fluids, meaning that heat exchangers can effectively cool as well as heat fluid—they are often used in refrigeration applications. Because plate heat exchangers have such a large surface area.
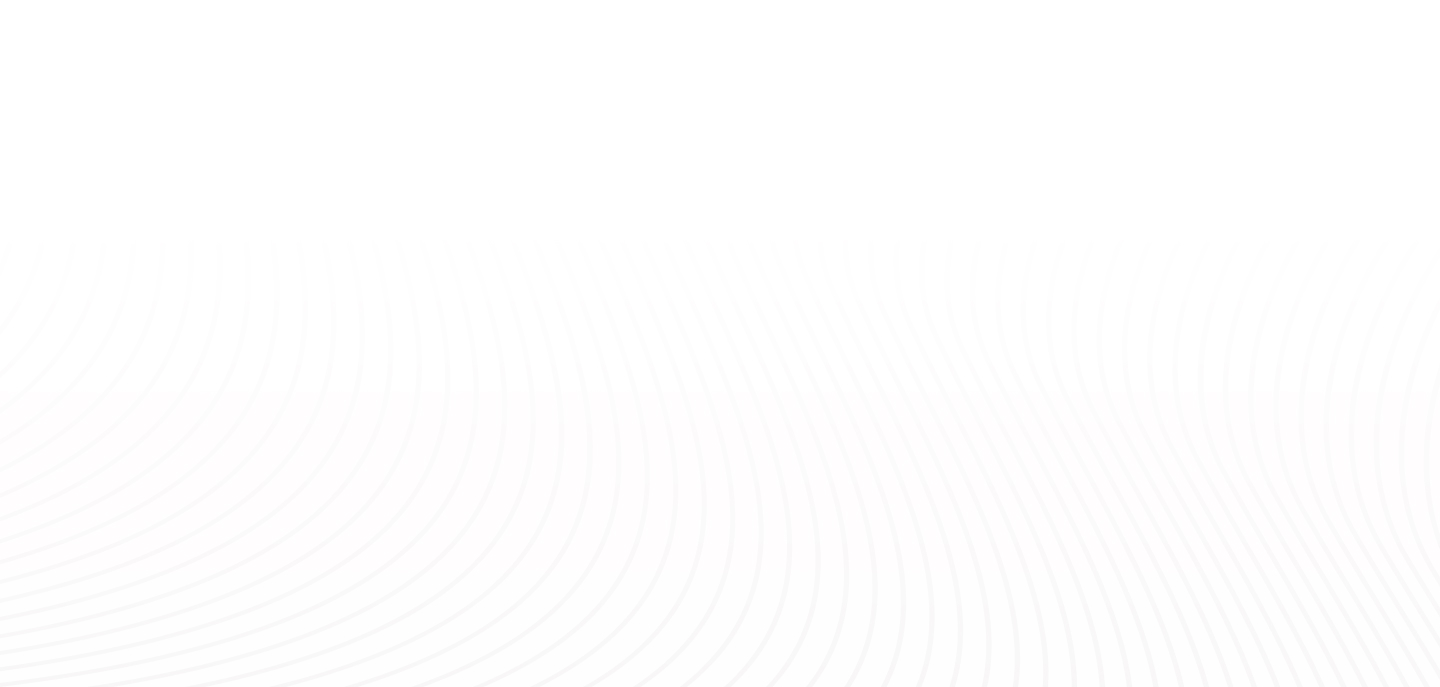
We are a dynamic privately owned organization located in Iran, (Shiraz Especial Economic Zone) having a leading vision in the practices of providing engineering solutions for a wide array of market sectors such as Oil & Gas, Refining, Chemical & Petrochemical, and Water industries. Our Main Solutions are Heat Transfer, Under Pressure & Storage Vessels, Agitation & Mixing, Filtration & Separation and Custom Designed Skid Mounted Process Units.
+98-21-48814000~3 / +98-71-91005567
sales@farnikan.com / info@farnikan.com
Office: Flat# 706, Hamila Building, No. 38, Hamila Blv., Pounak, Tehran, Iran.
Factory: No. 17, Sanat 6 Street, Shiraz Especial Economic Zone, Shiraz, Iran.
Factory: No. 17, Sanat 6 Street, Shiraz Especial Economic Zone, Shiraz, Iran.
Office: Flat# 706, Hamila Building, No. 38, Hamila Blv., Pounak Tehran, Iran.